Planar parallel mechanism end tracking control system based on two-dimensional encoder and planar parallel mechanism end tracking control method thereof
A technology of two-dimensional coding and tracking control, which is applied in the general control system, control/regulation system, computer control, etc., can solve the problems of high installation accuracy, time-consuming, and low measurement accuracy, and achieve good real-time performance and improved Effects of Positioning Accuracy and Tracking Accuracy
- Summary
- Abstract
- Description
- Claims
- Application Information
AI Technical Summary
Problems solved by technology
Method used
Image
Examples
Embodiment Construction
[0029] The present invention will be described in detail below in conjunction with the accompanying drawings and specific embodiments.
[0030] A two-dimensional encoder-based end tracking control system for planar parallel mechanisms, such as Figure 1-5 As shown, it includes a plane parallel mechanism installed on a static platform, a two-dimensional encoder measuring device, a mechanism zero return device and a control device.
[0031]The two-dimensional encoder measuring device of the present invention includes a reading head 6 and b reading head 16 of the two-dimensional encoder, a two-dimensional grating plate 15 in the two-dimensional grating plate fixture 14, and a connecting cable; wherein, the two-dimensional encoder A reading head 6 and b reading head 16 are fixed on the support frame 7 connected to the opposite side of the planar parallel mechanism actuating platform 5, and the two-dimensional grating plate fixture 14 equipped with a two-dimensional grating plate 1...
PUM
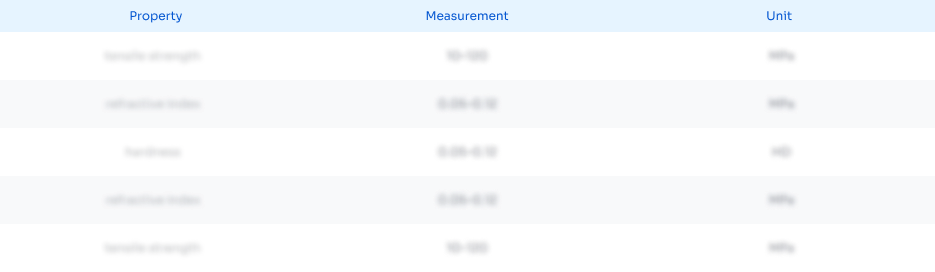
Abstract
Description
Claims
Application Information

- R&D
- Intellectual Property
- Life Sciences
- Materials
- Tech Scout
- Unparalleled Data Quality
- Higher Quality Content
- 60% Fewer Hallucinations
Browse by: Latest US Patents, China's latest patents, Technical Efficacy Thesaurus, Application Domain, Technology Topic, Popular Technical Reports.
© 2025 PatSnap. All rights reserved.Legal|Privacy policy|Modern Slavery Act Transparency Statement|Sitemap|About US| Contact US: help@patsnap.com