Movable assembling mechanism based on joint robot
An assembly mechanism and robot technology, applied in the direction of manipulators, manufacturing tools, etc., can solve the problems of incapable of real-time monitoring of working status, incapable of large-scale application, low accuracy of workpiece positioning, etc., to achieve convenient real-time monitoring and maintenance, and a wide range of applications , The connection is stable and firm
- Summary
- Abstract
- Description
- Claims
- Application Information
AI Technical Summary
Problems solved by technology
Method used
Image
Examples
Embodiment 1
[0026] Such as figure 1 As shown, a movable assembly mechanism based on a joint robot in this embodiment includes: a body 1, a first manipulator 2, a second manipulator 3, a third manipulator 4, an up and down transplanting electric cylinder 5, a motor 6, Coupling 7, screw rod 8, sleeve 9, spring 10, vision sensor 11, handheld programmer 12, control panel 13, tool box 14 and pulley 15.
[0027] The connection relationship of the above-mentioned components is as follows: the first manipulator 2 is fixed on the inner wall of the fuselage 1, the second manipulator 3 slides back and forth on the slide rail provided by the first manipulator 2, and the third manipulator 4 The second manipulator 3 slides forward and backward on the slide rail; the third manipulator 4 is connected with the up and down transplanting electric cylinder 5 and the visual sensor 11 in turn, and the motor 6 and the screw rod 8 pass through the coupling 7 provided between the two. It is slidingly connected w...
PUM
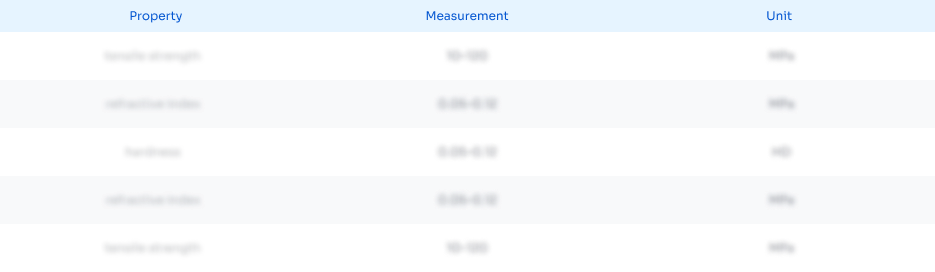
Abstract
Description
Claims
Application Information

- R&D
- Intellectual Property
- Life Sciences
- Materials
- Tech Scout
- Unparalleled Data Quality
- Higher Quality Content
- 60% Fewer Hallucinations
Browse by: Latest US Patents, China's latest patents, Technical Efficacy Thesaurus, Application Domain, Technology Topic, Popular Technical Reports.
© 2025 PatSnap. All rights reserved.Legal|Privacy policy|Modern Slavery Act Transparency Statement|Sitemap|About US| Contact US: help@patsnap.com