Fluid dynamic pressure type mechanical sealing face structure
A mechanical seal and hydrodynamic pressure technology, which is applied to the sealing of engines, liquid fuel engines, mechanical equipment, etc., can solve the problems of dry grinding of sealing surfaces, peaks of oblique corrugated surfaces equal to the theoretical surface, and insufficient thickness of liquid film. To achieve the effect of sealing function, novel design and simple structure
- Summary
- Abstract
- Description
- Claims
- Application Information
AI Technical Summary
Problems solved by technology
Method used
Image
Examples
Embodiment Construction
[0024] The invention proposes a new end face structure of a hydrodynamic mechanical seal for a nuclear main pump. see figure 1 , the static ring 10 of the hydrodynamic mechanical seal structure of the present invention has 12 grooves 11 on its sealing end surface, which are connected to form a regular dodecagon, and the center of the regular dodecagon is connected to the static ring. The center of the ring 10 is concentric. As can be seen from the partial enlarged view on the right, each groove 11 is a millimeter-scale rectangular groove.
[0025] These 12 grooves 11 communicate with each other, and the connection between any two adjacent grooves 11 is connected with the outer circumferential surface of the static ring 10, which not only ensures the introduction of high-pressure fluid required for the generation of liquid film by hydrodynamic pressure , At the same time, the high-pressure fluid volume is increased, which can better realize the force uniformity and liquid fil...
PUM
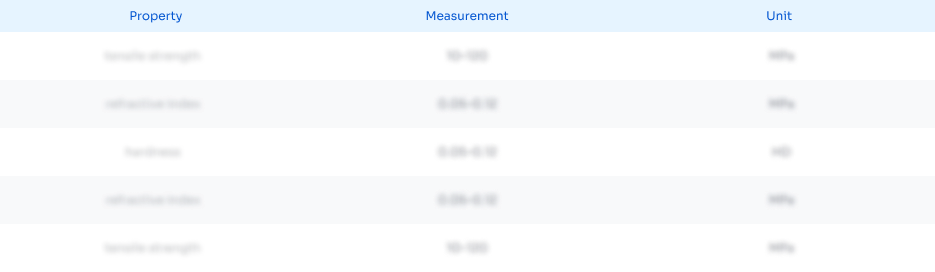
Abstract
Description
Claims
Application Information

- R&D
- Intellectual Property
- Life Sciences
- Materials
- Tech Scout
- Unparalleled Data Quality
- Higher Quality Content
- 60% Fewer Hallucinations
Browse by: Latest US Patents, China's latest patents, Technical Efficacy Thesaurus, Application Domain, Technology Topic, Popular Technical Reports.
© 2025 PatSnap. All rights reserved.Legal|Privacy policy|Modern Slavery Act Transparency Statement|Sitemap|About US| Contact US: help@patsnap.com