Weld head
A welding head and spot welding technology, used in welding equipment, resistance welding equipment, manufacturing tools, etc., can solve problems such as mutual collision, damage, and wear of electrodes
- Summary
- Abstract
- Description
- Claims
- Application Information
AI Technical Summary
Problems solved by technology
Method used
Image
Examples
Embodiment Construction
[0012] The present disclosure relates to various embodiments of a horn configured as a pair of opposing electrodes pressed against opposite sides of a component or a pair of side-by-side electrodes pressed against the surface of one or more of the components. Electrodes supply electric current to spot weld two or more parts together. Additionally, embodiments of the horn of the present disclosure are configured to compensate for operating temperature changes or fluctuations within a linear actuation motor configured to push the position of one or both electrodes. Furthermore, embodiments of the horn are configured to compensate for variations in the magnetic field strength of the magnets housed in the linear actuation motor. Embodiments of the horn of the present disclosure also include a detent configured to lock the position of the electrodes when the horn is powered off, thereby preventing the electrodes from striking each other, which could otherwise damage or prematurely ...
PUM
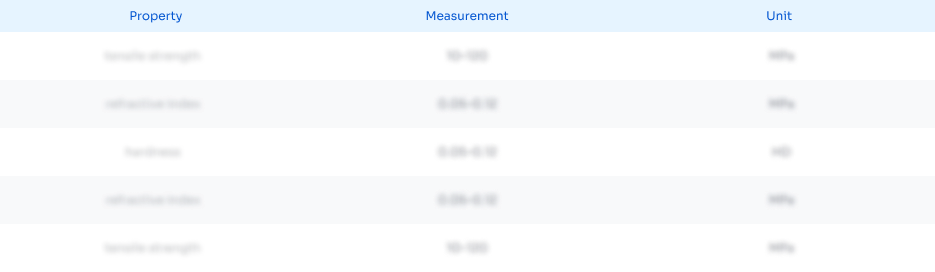
Abstract
Description
Claims
Application Information

- Generate Ideas
- Intellectual Property
- Life Sciences
- Materials
- Tech Scout
- Unparalleled Data Quality
- Higher Quality Content
- 60% Fewer Hallucinations
Browse by: Latest US Patents, China's latest patents, Technical Efficacy Thesaurus, Application Domain, Technology Topic, Popular Technical Reports.
© 2025 PatSnap. All rights reserved.Legal|Privacy policy|Modern Slavery Act Transparency Statement|Sitemap|About US| Contact US: help@patsnap.com