Automatic locating device, bender system employing automatic locating device and plate bending method
An automatic positioning and bending machine technology, applied in the field of bending machines, can solve the problems of inflexible use, high manufacturing cost, inconvenient promotion and application, etc., and achieve the effects of flexible use, reduced energy consumption, and improved bending efficiency
- Summary
- Abstract
- Description
- Claims
- Application Information
AI Technical Summary
Problems solved by technology
Method used
Image
Examples
Embodiment 1
[0045] combine figure 2 , image 3 with Figure 4 , a kind of automatic positioning device of the present embodiment, comprises automatic elevating mechanism and workbench, and described automatic elevating mechanism comprises support 31, elevating frame, fixed plate 33, sliding plate 34 and slider guide rail 35, support 31, elevating frame , fixed plate 33, sliding plate 34 and slider guide rail 35 are all arranged in pairs, support 31 supports elevating frame, elevating frame is connected with fixed plate 33, fixed plate 33 and sliding plate 34 surround a square frame, two sliding plates 34 are opposite Set and can move along the length direction of the fixed plate 33; the two slider guide rails 35 are arranged in the middle of the fixed plate 33, and the slider guide rails 35 are parallel to the slide plate 34, and the slider guide rails 35 are provided with sliders 351, the slider 351 can move along the slider guide rail 35.
[0046] In the present embodiment, the two ...
Embodiment 2
[0052] A bending machine system in this embodiment includes the automatic positioning device as described in Embodiment 1, and also includes figure 1 The shown automatic feeding mechanism and a bending machine 5, the automatic feeding mechanism includes a feeding manipulator 1, one end of the feeding manipulator 1 is provided with a suction cup group 11, and the suction cup group 11 is arranged in a circle by a plurality of suction cups . The bending machine 5 is arranged on the side perpendicular to the moving direction of the sliding block 351 of the automatic positioning device.
[0053] The structural block diagram of the control system and the electrical control schematic diagram of the present embodiment are as follows: Figure 5 with Image 6 As shown, the process of sheet metal bending is:
[0054] Step 1. The feeding manipulator 1 absorbs the workpiece 2 and puts it on the workbench plane 6;
[0055] Step 2, the servo motor controls the lifting frame to rise, and ...
Embodiment 3
[0062] A bending machine system of this embodiment is basically the same as that of Embodiment 1, the difference is that two bending machines 5 are provided in this embodiment, and the two bending machines 5 are respectively arranged on the automatic positioning device and the slide Block 351 moves both sides perpendicular to the direction.
[0063] The working process of this embodiment is as follows: first, the workpiece 2 is adsorbed by the loading manipulator 1 to the workbench, and placed on a certain area of the workbench. When the feeding manipulator 1 absorbs the workpiece 2 to the workbench, the 3# servo motor 43 and the 4# servo motor 44 start at the same time, driving the automatic lifting mechanism to move upward until the automatic lifting mechanism completely fits the workbench. At this time, the sliding plate 34 The two sides of the workbench rise to the top of the workbench, and the height is slightly higher than the workbench plane 6 . The slider 351 is inse...
PUM
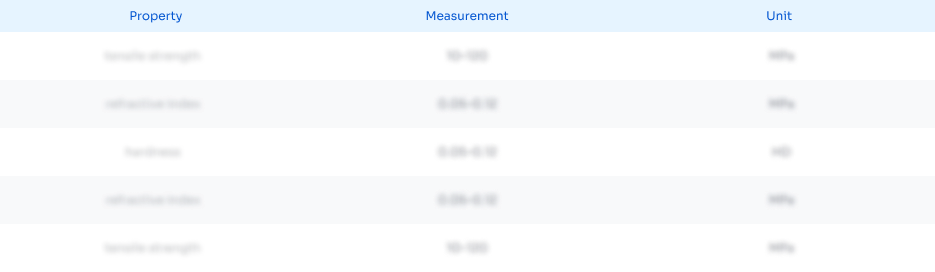
Abstract
Description
Claims
Application Information

- Generate Ideas
- Intellectual Property
- Life Sciences
- Materials
- Tech Scout
- Unparalleled Data Quality
- Higher Quality Content
- 60% Fewer Hallucinations
Browse by: Latest US Patents, China's latest patents, Technical Efficacy Thesaurus, Application Domain, Technology Topic, Popular Technical Reports.
© 2025 PatSnap. All rights reserved.Legal|Privacy policy|Modern Slavery Act Transparency Statement|Sitemap|About US| Contact US: help@patsnap.com