Friction-piezoelectricity-magnetoelectricity composite vibration miniature energy collector
A composite, micro-energy technology, applied in the direction of piezoelectric effect/electrostrictive or magnetostrictive motors, friction generators, generators/motors, etc., can solve the problems of inability to achieve efficient collection and dissipation of mechanical energy, To achieve the effect of enriching application occasions, high energy collection efficiency, and good market application value
- Summary
- Abstract
- Description
- Claims
- Application Information
AI Technical Summary
Problems solved by technology
Method used
Image
Examples
Embodiment Construction
[0013] Specific embodiments of the present invention will be described in detail below in conjunction with the accompanying drawings.
[0014] A friction-piezoelectric-magnetoelectric composite single-degree-of-freedom vibration micro-energy harvester, such as figure 1 , 2 As shown, it includes a magnetic levitation support frame 8 located in the middle, and a floating fixed magnet post 9 is placed in the magnet placement cavity around the edge of the magnetic levitation support frame 8, and a magnet support 12 is placed in the central cavity of the magnetic levitation support frame 8. The floating magnet 11 is fixed in the magnet bracket 12; the upper and lower sides of the magnetic levitation support frame 8 are respectively provided with a friction film 10, and the back side of the friction film 10 is covered with a layer of electrodes and lead wires; the upper and lower layers of the friction film 10 are respectively fixed on On the electromagnetic induction coils 7 of th...
PUM
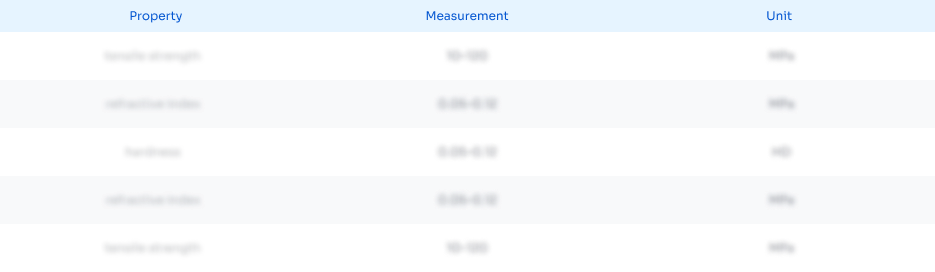
Abstract
Description
Claims
Application Information

- R&D Engineer
- R&D Manager
- IP Professional
- Industry Leading Data Capabilities
- Powerful AI technology
- Patent DNA Extraction
Browse by: Latest US Patents, China's latest patents, Technical Efficacy Thesaurus, Application Domain, Technology Topic, Popular Technical Reports.
© 2024 PatSnap. All rights reserved.Legal|Privacy policy|Modern Slavery Act Transparency Statement|Sitemap|About US| Contact US: help@patsnap.com