Magnetic sensor
一种磁传感器、磁场的技术,应用在磁传感器领域,能够解决MR元件磁阻变化率下降、自由层矫顽力增加、MR元件线性变差等问题
- Summary
- Abstract
- Description
- Claims
- Application Information
AI Technical Summary
Problems solved by technology
Method used
Image
Examples
no. 1 approach
[0032] Hereinafter, embodiments of the present invention will be described with reference to the drawings. First, refer to figure 1 , an example of a magnetic sensor system including the magnetic sensor according to the first embodiment of the present invention will be described. figure 1 It is a perspective view showing the structure of the magnetic sensor system of this embodiment. figure 1 The illustrated magnetic sensor system includes the magnetic sensor 1 of the present embodiment and a rotation scale 50 that generates a magnetic field of an object detected by the magnetic sensor 1 . The rotary scale 50 rotates along a rotation direction D around a predetermined central axis C in conjunction with an unillustrated operating body that rotates. As a result, the relative positional relationship between the rotary scale 50 and the magnetic sensor 1 changes in the rotational direction D. As shown in FIG. The magnetic sensing system detects physical quantities related to the...
no. 2 approach
[0087] Next, refer to Figure 13 , the second embodiment of the present invention will be described. Figure 13 It is an enlarged side view showing a part of the magnetic sensor of this embodiment. The magnetic sensor 1 of the present embodiment includes eight MR elements 10, four bias magnetic field generators 20, a substrate not shown, two upper electrodes (first electrodes) 30, and two lower electrodes (second electrodes). 40. In this embodiment, two MR elements 10 connected in parallel via upper electrode 30 and lower electrode 40 are arranged at respective positions of MR elements 10A, 10B, 10C, and 10D described in the first embodiment.
[0088] In the present embodiment, the two MR elements 10 connected in parallel are arranged such that at least a part of each of the two MR elements 10 is contained in the space S defined by the corresponding bias magnetic field generator 20 . The magnetization directions of the magnetization fixed layers 13 in the two MR elements 10...
PUM
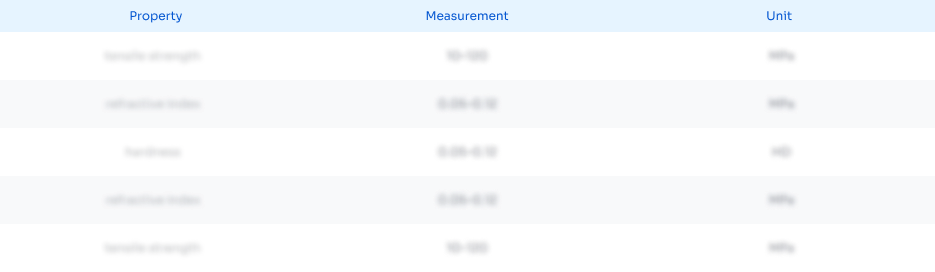
Abstract
Description
Claims
Application Information

- R&D
- Intellectual Property
- Life Sciences
- Materials
- Tech Scout
- Unparalleled Data Quality
- Higher Quality Content
- 60% Fewer Hallucinations
Browse by: Latest US Patents, China's latest patents, Technical Efficacy Thesaurus, Application Domain, Technology Topic, Popular Technical Reports.
© 2025 PatSnap. All rights reserved.Legal|Privacy policy|Modern Slavery Act Transparency Statement|Sitemap|About US| Contact US: help@patsnap.com