Method and system for acquiring PID (Proportion Integration Differentiation) self-tuning parameter of positioner
A parameter acquisition and self-tuning technology, which is applied to complex mathematical operations, valve details, engine components, etc., can solve problems such as excessive time-consuming, complicated positioner self-tuning methods, and affecting the normal operation of controlled devices to achieve accurate records , PID parameter calculation accurate effect
- Summary
- Abstract
- Description
- Claims
- Application Information
AI Technical Summary
Problems solved by technology
Method used
Image
Examples
Embodiment 1
[0032] Embodiment 1: a method for obtaining locator PID self-tuning parameters, comprising the following steps,
[0033] S100: a step of adjusting the regulating valve to a preset opening degree;
[0034] S200: a step of oscillating the regulating valve up and down the preset opening according to the preset amplitude a;
[0035] S300: A step of detecting the actual opening of the regulating valve; the step of detecting the actual opening of the regulating valve includes the steps of filtering and amplifying the collected regulating valve opening information and performing AD conversion.
[0036] S400: After the regulating valve starts to oscillate and adjust, the parameters of the first three oscillating cycles are discarded and not recorded. The time t when the actual opening of the regulating valve > the preset opening in one oscillation cycle 高n , and the actual opening of the regulating valve in each oscillation cycle 低n ;
[0037] Specifically, in this step, include, ...
Embodiment 2
[0048] Embodiment 2: as figure 1 As shown, this embodiment provides a positioner PID self-tuning parameter acquisition system, including a given control module 1, a regulating valve 2, a feedback module 3, a detection and comparison module 4, a level output circuit 5 and a timer 6 connected in sequence ; The detection and comparison module 4 and the timer 6 are also connected to a calculation module 7 at the same time;
[0049] The given control module 1 is used to control the regulating valve 2 to oscillate and adjust at a preset opening up and down according to a preset amplitude;
[0050] The feedback module 3 is used to collect the actual opening of the regulating valve 2;
[0051] The detection and comparison module 4 is used to receive the actual opening degree of the regulating valve 2 fed back by the feedback module, and control the level output circuit 5 to change the output level when judging that the actual opening degree is equal to the preset opening degree; at the...
PUM
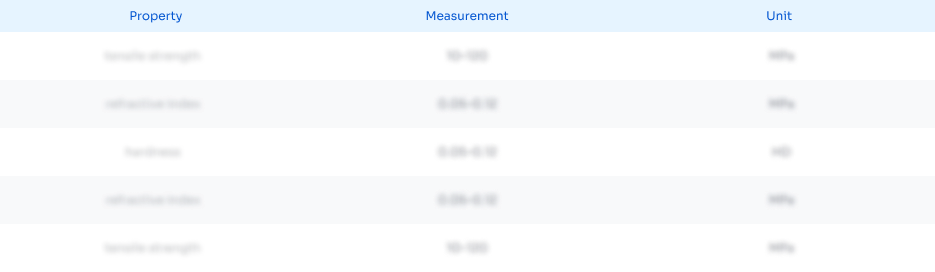
Abstract
Description
Claims
Application Information

- R&D
- Intellectual Property
- Life Sciences
- Materials
- Tech Scout
- Unparalleled Data Quality
- Higher Quality Content
- 60% Fewer Hallucinations
Browse by: Latest US Patents, China's latest patents, Technical Efficacy Thesaurus, Application Domain, Technology Topic, Popular Technical Reports.
© 2025 PatSnap. All rights reserved.Legal|Privacy policy|Modern Slavery Act Transparency Statement|Sitemap|About US| Contact US: help@patsnap.com