Curve-welding-seam three-dimensional reconstruction method based on line structure light vision detection
A linear structured light and visual inspection technology, applied in measurement devices, optical devices, instruments, etc., can solve the problems of low efficiency of contact detection devices, increasing the complexity of welding seam inspection algorithms, and the impact of reliable inspection of welding seams.
- Summary
- Abstract
- Description
- Claims
- Application Information
AI Technical Summary
Problems solved by technology
Method used
Image
Examples
Embodiment Construction
[0028] Such as Figure 1 ~ Figure 4 As shown, a three-dimensional reconstruction method for curved weld seams based on line structured light vision detection, which includes a robotic arm 1, a line structured light vision system, a controller 2 connected to the robotic arm 1, a computer 3 connected to the controller 2, and a line structured light vision system. The vision system includes a camera 4 and a wire structured light projector 5. The camera 4 is fixed at the end of the mechanical arm 1. The wire structured light projector 5 is fixed on one side of the camera 4 and projected on the surface of the workpiece 6 to be welded, forming an eye-in-hand (Eye-in-Hand) system, as a machine vision device for detection and measurement, the line structured light projector 5 can project single-line or multi-line structured light onto the surface of the workpiece to be welded, and the camera 4 is used to collect structured light projection images, And transmit the image to an image pr...
PUM
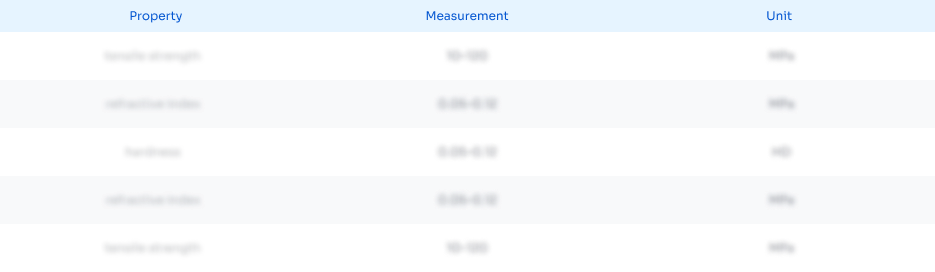
Abstract
Description
Claims
Application Information

- R&D
- Intellectual Property
- Life Sciences
- Materials
- Tech Scout
- Unparalleled Data Quality
- Higher Quality Content
- 60% Fewer Hallucinations
Browse by: Latest US Patents, China's latest patents, Technical Efficacy Thesaurus, Application Domain, Technology Topic, Popular Technical Reports.
© 2025 PatSnap. All rights reserved.Legal|Privacy policy|Modern Slavery Act Transparency Statement|Sitemap|About US| Contact US: help@patsnap.com