Method for producing built-in biradial permanent magnet steel resultant magnetic field driving motor rotor
A technology for synthesizing a magnetic field and driving a motor. It is used in the manufacture of motor generators, magnetic circuit rotating parts, and stator/rotor bodies. It can solve the problems of irreversible demagnetization, reduction of drive motor efficiency, and decline, and achieve compact structure and magnetic field. The effect of high strength and high output power
- Summary
- Abstract
- Description
- Claims
- Application Information
AI Technical Summary
Problems solved by technology
Method used
Image
Examples
Embodiment Construction
[0008] The present invention will be further described below in conjunction with accompanying drawing:
[0009] The production method of the motor rotor driven by built-in double radial permanent magnet steel synthetic magnetic field is characterized in that: punching and cutting circular rotor punches, the rotor punches are uniformly distributed with an even number of punches that penetrate the thickness of the rotor punches and are formed by two first rectangular slots The inverted "eight"-shaped grooves, the outer ends of the two adjacent first rectangular grooves forming the inverted "eight"-shaped grooves are not connected, the minimum size of the disconnected part is 1.5mm, the inverted shape formed by the two first rectangular grooves In the middle of the inner end of the "eight"-shaped groove, there is a positive "eight"-shaped groove that runs through the thickness of the rotor punch and is formed by two second rectangular grooves, and the outer ends of the two second ...
PUM
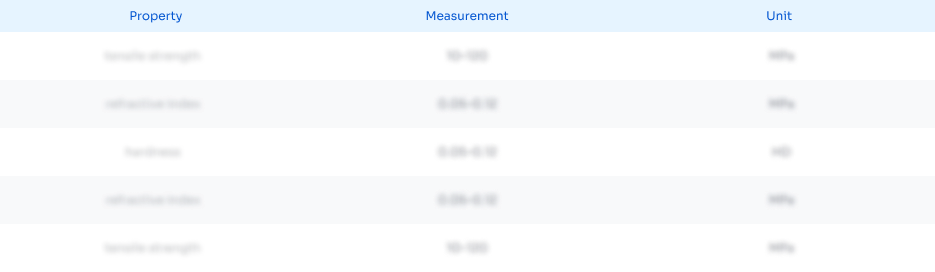
Abstract
Description
Claims
Application Information

- Generate Ideas
- Intellectual Property
- Life Sciences
- Materials
- Tech Scout
- Unparalleled Data Quality
- Higher Quality Content
- 60% Fewer Hallucinations
Browse by: Latest US Patents, China's latest patents, Technical Efficacy Thesaurus, Application Domain, Technology Topic, Popular Technical Reports.
© 2025 PatSnap. All rights reserved.Legal|Privacy policy|Modern Slavery Act Transparency Statement|Sitemap|About US| Contact US: help@patsnap.com