Operating method on basis of master-slave industrial robot collaboration
A technology for industrial robots and operations, applied in the direction of instruments, manipulators, manufacturing tools, etc., can solve the problem of high economic cost
- Summary
- Abstract
- Description
- Claims
- Application Information
AI Technical Summary
Problems solved by technology
Method used
Image
Examples
Embodiment 1
[0159] Embodiment 1——Collaborative Handling Experiment
[0160] The collaborative handling experiment is to first control the master-slave industrial robot to grab the target rigid body, then control the movement of the master industrial robot, and drive the slave industrial robot to coordinate with the master industrial robot to carry the rigid body together. The specific steps are as follows: ① Put the master-slave industrial robot ②Start the simulation and control software; ③Select the control mode (control mode and simulation mode) and cooperation mode; ④Control the main industrial robot to grab the steel rod; ⑤Control the slave industrial robot to grab the steel rod; ⑥Control the master-slave industrial robot to carry the steel bar to the target position; ⑦The master industrial robot and the slave industrial robot release the manipulator respectively; ⑧Reset both the master-slave industrial robot; When transporting a rigid body, choose a different path each time to reach ...
Embodiment 2
[0162] Embodiment 2——Collaborative assembly experiment
[0163] The collaborative assembly experiment is roughly divided into two steps according to its task decomposition, one is to grasp the target, and the other is to assemble. First, control two industrial robots to grab the shaft and hole (replaced by steel rod and sleeve here), and move the shaft and hole to the pre-assembly pose respectively, and then complete the shaft according to the size of the shaft hole and the assembly speed. Hole assembly task, the specific experimental steps are as follows: ① Select the control mode (control mode and simulation mode) and cooperation mode. ② Control the main industrial robot to grab the steel rod. ③Control the industrial robot to grab the rod cover. ④ The master and slave industrial robots move to the pre-assembly pose respectively. ⑤ Start assembling the shaft and the hole. ⑥ Put the assembled shaft hole in the target pose. ⑦ Both master and slave industrial robots are res...
PUM
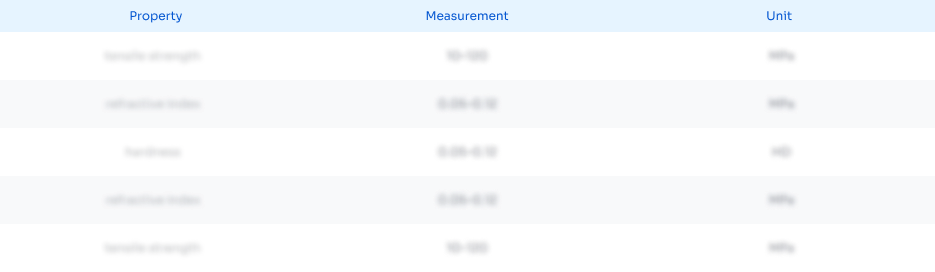
Abstract
Description
Claims
Application Information

- R&D
- Intellectual Property
- Life Sciences
- Materials
- Tech Scout
- Unparalleled Data Quality
- Higher Quality Content
- 60% Fewer Hallucinations
Browse by: Latest US Patents, China's latest patents, Technical Efficacy Thesaurus, Application Domain, Technology Topic, Popular Technical Reports.
© 2025 PatSnap. All rights reserved.Legal|Privacy policy|Modern Slavery Act Transparency Statement|Sitemap|About US| Contact US: help@patsnap.com