Graphene in-situ modified polyurethane and method for manufacturing synthetic leather with high physical properties
A technology of graphene modification and in-situ modification, which is applied in textiles and papermaking, can solve the problems of inability to improve the performance of polyurethane and synthetic leather, and achieve obvious innovation, improve quality level, and improve heat resistance. Effect
- Summary
- Abstract
- Description
- Claims
- Application Information
AI Technical Summary
Problems solved by technology
Method used
Examples
Embodiment 1
[0031] Embodiment 1: the manufacture of dry process vamp synthetic leather
[0032] (1) Modification of graphene (parts by weight)
[0033] Add 10 parts of enhanced graphene to 90 parts of propylene glycol methyl ether acetate, add 10 parts of KH-550 silicone coupling agent, and react at 70°C for 24 hours to obtain lipophilic modified graphene;
[0034] (2) Preparation of graphene in-situ modified polyurethane slurry (parts by weight);
[0035] ①Preparation of surface treatment agent: Add 1.0 parts of modified graphene to 100 parts of polyurethane for surface treatment with a solid content of 20%, and mix evenly with additives such as wetting and leveling agent, defoamer, thickener, and color paste , to obtain a surface treatment agent for in-situ modification of graphene;
[0036] ② Preparation of surface layer slurry: Add 0.5 parts of modified graphene to 100 parts of polyurethane solution for surface layer with a solid content of 30%, and mix appropriate amount of additiv...
Embodiment 2
[0042] Embodiment 2: the manufacture of wet method sofa synthetic leather
[0043] (1) Modification of graphene (parts by weight)
[0044] Add 5 parts of enhanced graphene and 5 parts of thermally conductive graphene to 90 parts of dimethylformamide, add 5 parts of KH-560 silicone coupling agent, and react at 70°C for 24 hours to obtain lipophilic modified graphene ;
[0045] (2) Preparation of graphene in-situ modified polyurethane slurry (parts by weight);
[0046] ①Preparation of surface treatment agent: Add 0.8 parts of modified graphene to 100 parts of polyurethane for surface treatment with a solid content of 25%, and mix evenly with additives such as wetting and leveling agent, defoamer, thickener, and color paste , to obtain a surface treatment agent for in-situ modification of graphene;
[0047] ② Preparation of surface layer slurry: Add 0.4 parts of modified graphene to 100 parts of polyurethane solution for surface layer with a solid content of 30%, and mix appro...
Embodiment 3
[0053] Embodiment 3: the manufacture of dry method automobile cushion leather
[0054] (1) Modification of graphene (parts by weight)
[0055] Add 10 parts of enhanced graphene to 45 parts of propylene dimethyl formamide and 45 parts of glycol methyl ether acetate, add 10 parts of KH-602 silicone coupling agent, and react at 70°C for 24 hours to obtain lipophilic modification Sexual graphene;
[0056] (2) Preparation of graphene in-situ modified polyurethane slurry (parts by weight);
[0057] ①Preparation of surface treatment agent: Add 0.7 parts of modified graphene to 100 parts of polyurethane for surface treatment with a solid content of 20%, and mix evenly with additives such as wetting and leveling agent, defoamer, thickener, and color paste , to obtain a surface treatment agent for in-situ modification of graphene;
[0058] ② Preparation of surface layer slurry: Add 0.5 parts of modified graphene to 100 parts of polyurethane solution for surface layer with a solid con...
PUM
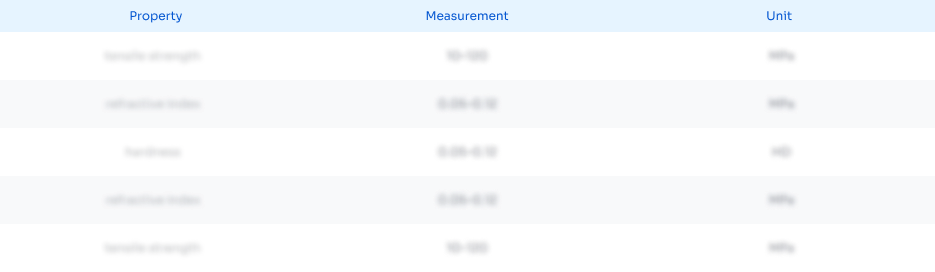
Abstract
Description
Claims
Application Information

- R&D
- Intellectual Property
- Life Sciences
- Materials
- Tech Scout
- Unparalleled Data Quality
- Higher Quality Content
- 60% Fewer Hallucinations
Browse by: Latest US Patents, China's latest patents, Technical Efficacy Thesaurus, Application Domain, Technology Topic, Popular Technical Reports.
© 2025 PatSnap. All rights reserved.Legal|Privacy policy|Modern Slavery Act Transparency Statement|Sitemap|About US| Contact US: help@patsnap.com