Reducing force measurement cable arrangement structure
A cable arranging mechanism and force measurement technology, applied in the direction of the spring mechanism and the hoisting device, can solve the problems of reduced service life, small bending radius of the cable, affecting the measurement results, etc., to prevent stress concentration or damage, and meet the measurement requirements. Force and cable arrangement requirements, the effect of improving measurement accuracy
- Summary
- Abstract
- Description
- Claims
- Application Information
AI Technical Summary
Problems solved by technology
Method used
Image
Examples
Embodiment Construction
[0031] A variable-diameter force-measuring cable-discharging mechanism of the present invention will be further described below in conjunction with the accompanying drawings and specific embodiments:
[0032] Such as Figure 6 , Figure 7 and Figure 9As shown, a variable-diameter force-measuring cable-discharging mechanism of the present invention includes a winch cable reel 1, a cable-receiving gear motor 2, a cable reel left support 3, a cable reel right support 4, a cable-discharging unit and a variable-diameter force-measuring unit. The cable take-up deceleration motor 2 is installed on the cable reel left bracket 3, the output shaft of the take-up deceleration motor 2 is connected with the winch cable reel 1, and the winch cable reel 1 is rotatably connected to the cable reel left support 3 and the cable reel right support 4 through bearings between. The cable discharge unit includes a cable discharge motor 8, a cable discharge bracket 5, a cable discharge guide rail ...
PUM
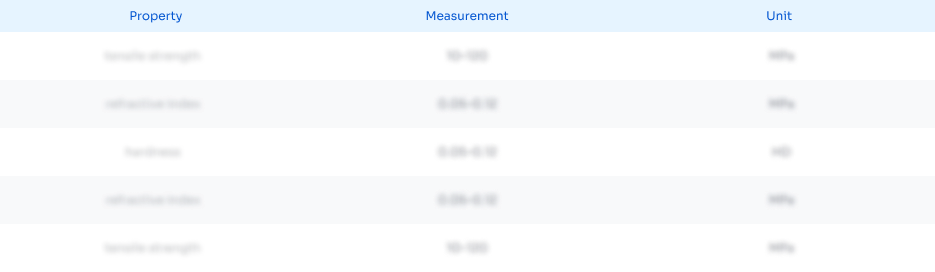
Abstract
Description
Claims
Application Information

- R&D Engineer
- R&D Manager
- IP Professional
- Industry Leading Data Capabilities
- Powerful AI technology
- Patent DNA Extraction
Browse by: Latest US Patents, China's latest patents, Technical Efficacy Thesaurus, Application Domain, Technology Topic.
© 2024 PatSnap. All rights reserved.Legal|Privacy policy|Modern Slavery Act Transparency Statement|Sitemap