An adjustable hip joint testing machine loading system
A loading system and hip joint technology, applied in the mechanical field, can solve the problems of difficult control, loading lag, and high cost, and achieve the effects of improving work efficiency, improving accuracy, and simple structure
- Summary
- Abstract
- Description
- Claims
- Application Information
AI Technical Summary
Problems solved by technology
Method used
Image
Examples
Embodiment Construction
[0029] The present invention will be further described below in conjunction with the accompanying drawings.
[0030] as attached figure 1 The Adjustable Hip Tester Loading System shown includes:
[0031] Power unit 1, used to generate test loading torque;
[0032] The loading force executing unit 5 is used to convert the torque into the loading force, and apply the loading force to the hip joint test material;
[0033] The magnetic coupling unit 3 is used to softly connect the power unit 1 and the loading force execution unit 5;
[0034] The hydraulic control unit 8 is used to drive the power unit 1 to perform feed movement, adjust the output torque of the magnetic coupling unit 3, and generate different loading forces;
[0035] The sensor detection feedback unit 7 is used to detect the real-time loading force and provide feedback for the micro-adjustment of the hydraulic control unit 8;
[0036] The main control unit 9 is used for collecting and analyzing the signal of th...
PUM
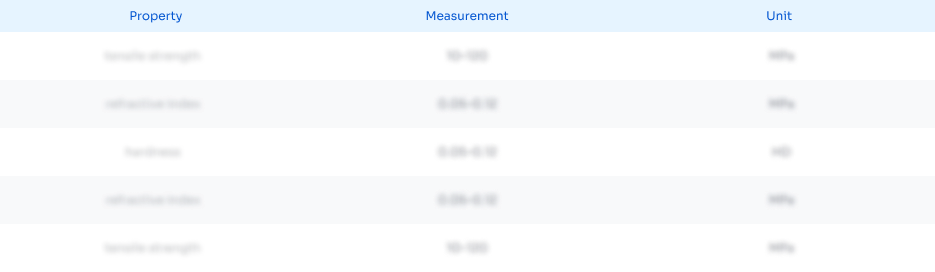
Abstract
Description
Claims
Application Information

- R&D Engineer
- R&D Manager
- IP Professional
- Industry Leading Data Capabilities
- Powerful AI technology
- Patent DNA Extraction
Browse by: Latest US Patents, China's latest patents, Technical Efficacy Thesaurus, Application Domain, Technology Topic, Popular Technical Reports.
© 2024 PatSnap. All rights reserved.Legal|Privacy policy|Modern Slavery Act Transparency Statement|Sitemap|About US| Contact US: help@patsnap.com