Base coordinate system calibration method of aircraft panel horizontal automatic drill riveter
A technology of automatic drilling and riveting machine and base coordinate system, which is applied in the direction of measuring devices, instruments, optical devices, etc., can solve the problems of increasing error introduction and complex transmission path of coordinate system
- Summary
- Abstract
- Description
- Claims
- Application Information
AI Technical Summary
Problems solved by technology
Method used
Image
Examples
Embodiment Construction
[0058] Such as Figure 1-Figure 3 As shown, the horizontal automatic drilling and riveting machine for aircraft siding is composed of a hole-making and nail-inserting side machine tool 1 and an upsetting side machine tool 5, wherein the hole-making and nail-inserting side machine tool 1 is composed of a hole-making and nail-inserting side CNC positioning device 2 and a machine tool The hole inserting nail actuator 3 is composed, and the upsetting side machine tool 5 is composed of the upsetting side numerical control positioning device 4 and the upsetting head 6; the aircraft wall plate 8 is fixed by the wall plate tooling 7.
[0059] Such as Figure 4 As shown, each CNC positioning device in the horizontal automatic drilling and riveting machine for aircraft siding has five motion axes of X, Y, Z, A, and B. The structural composition of the drilling and riveting machine system is displayed in the form of a sub-coordinate system, and It shows the cooperative working state of ...
PUM
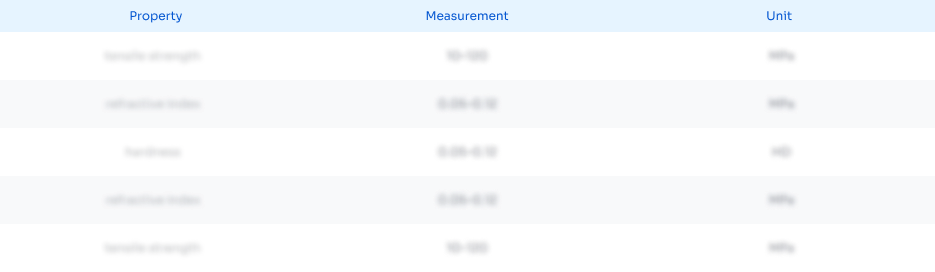
Abstract
Description
Claims
Application Information

- R&D
- Intellectual Property
- Life Sciences
- Materials
- Tech Scout
- Unparalleled Data Quality
- Higher Quality Content
- 60% Fewer Hallucinations
Browse by: Latest US Patents, China's latest patents, Technical Efficacy Thesaurus, Application Domain, Technology Topic, Popular Technical Reports.
© 2025 PatSnap. All rights reserved.Legal|Privacy policy|Modern Slavery Act Transparency Statement|Sitemap|About US| Contact US: help@patsnap.com