End surface groove machining forming equipment for bearing inner rings
A technology for bearing inner rings and forming equipment, applied in metal processing equipment, grinding/polishing equipment, manufacturing tools, etc., can solve problems such as high processing costs, low production efficiency, and inability to scale mass production
- Summary
- Abstract
- Description
- Claims
- Application Information
AI Technical Summary
Problems solved by technology
Method used
Image
Examples
Embodiment Construction
[0024] In order to make the object, technical solution and advantages of the present invention clearer, the present invention will be further described in detail below in conjunction with the accompanying drawings and embodiments. It should be understood that the specific embodiments described here are only used to explain the present invention, not to limit the present invention.
[0025] Please refer to Figure 1-5 , a bearing inner ring end surface groove processing and forming equipment of the present invention, including: a base 33, a column 1, a support frame 22, a grinding wheel distance adjustment mechanism, a power mechanism, a bearing inner ring feeding mechanism, and a cam intermittent mechanism. The column 1 and the support frame 22 are fixedly installed on the base 33 , the column 1 is provided with steps, and the base 33 is provided with a guide rail slider 40 .
[0026] The grinding wheel distance adjustment mechanism includes: hinged bushing 2, left hinged swi...
PUM
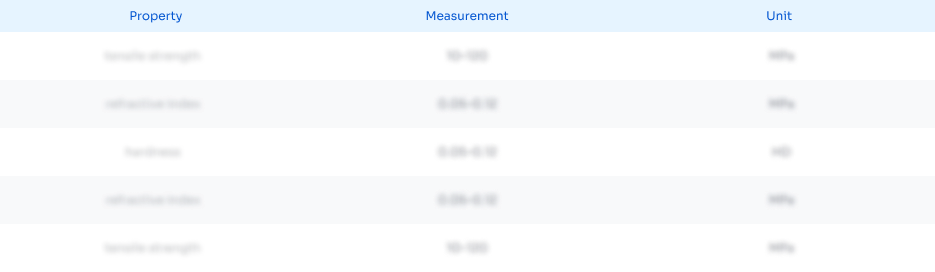
Abstract
Description
Claims
Application Information

- Generate Ideas
- Intellectual Property
- Life Sciences
- Materials
- Tech Scout
- Unparalleled Data Quality
- Higher Quality Content
- 60% Fewer Hallucinations
Browse by: Latest US Patents, China's latest patents, Technical Efficacy Thesaurus, Application Domain, Technology Topic, Popular Technical Reports.
© 2025 PatSnap. All rights reserved.Legal|Privacy policy|Modern Slavery Act Transparency Statement|Sitemap|About US| Contact US: help@patsnap.com