Spiral automated welding rolling machine for tanks
An automatic welding and can rolling machine technology, which is applied in the field of oil tank manufacturing, can solve the problems of welding undercut, slag inclusion, time-consuming, etc., and achieve the effects of improving production efficiency, reducing production land, and reducing process labor
- Summary
- Abstract
- Description
- Claims
- Application Information
AI Technical Summary
Problems solved by technology
Method used
Image
Examples
Embodiment Construction
[0032] Such as Figure 1-9 As shown, a spiral automatic welding can coiling machine includes a steel plate uncoiling device 1, a steel plate leveling device 2, a steel plate edge trimming device 3, a groove processing device 4, a delivery device 5 and a tube joint rolling device 6, the steel plate Uncoiling device 1, steel plate leveling device 2, steel plate edge trimming device 3, groove processing device 4, delivery device 5 and tube section rolling device 6 are arranged and installed in sequence, and one side of the tube section rolling device 6 is set There is a welding robot arm 7;
[0033] The steel plate uncoiling device 1 is used for uncoiling the roll-shaped steel plate, the steel plate leveling device 2 is used for leveling the uncoiled steel plate, and the steel plate edge trimming device 3 trims the edge of the steel plate after leveling, and trims the edge The finished steel plate is subjected to bevel treatment through the bevel treatment device 4, and the deli...
PUM
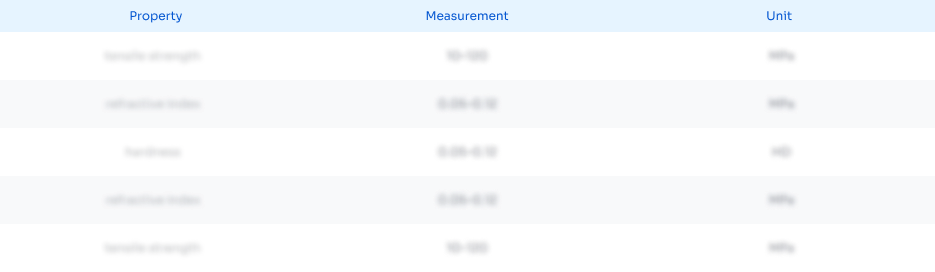
Abstract
Description
Claims
Application Information

- Generate Ideas
- Intellectual Property
- Life Sciences
- Materials
- Tech Scout
- Unparalleled Data Quality
- Higher Quality Content
- 60% Fewer Hallucinations
Browse by: Latest US Patents, China's latest patents, Technical Efficacy Thesaurus, Application Domain, Technology Topic, Popular Technical Reports.
© 2025 PatSnap. All rights reserved.Legal|Privacy policy|Modern Slavery Act Transparency Statement|Sitemap|About US| Contact US: help@patsnap.com