Antiaging torsion-resistant ethylene-propylene rubber for wires and cables and preparation method thereof
A technology of ethylene-propylene rubber, wire and cable, applied in the field of power cables, can solve the problems of ethylene-propylene rubber varieties and cable insulation requirements, etc., and achieve the effect of simple and feasible preparation method, good torsion performance, and easy promotion
- Summary
- Abstract
- Description
- Claims
- Application Information
AI Technical Summary
Problems solved by technology
Method used
Examples
Embodiment 1
[0022] Example 1: Preparation of ethylene propylene rubber
[0023] The proportion of raw materials by weight:
[0024] EPDM rubber, 90 parts; acrylic acid, 5 parts; p-aminobenzenesulfonic acid, 2 parts; ammonium persulfate, 1.5 parts; mercaptopropionic acid, 0.7 parts; phenyl-β-naphthylamine, 0.5 parts; initiator , 2 parts; anti-aging agent, 3 parts; flame retardant, 1.5 parts; a total of 0.5 parts of benzotriazole and sulfurized isobutylene; the weight ratio of benzotriazole and sulfurized isobutylene is 4:1.
[0025] Preparation:
[0026] Step S1, heating and premixing EPDM rubber, acrylic acid, p-aminobenzenesulfonic acid, ammonium persulfate, mercaptopropionic acid, phenyl-β-naphthylamine, benzotriazole and vulcanized isobutylene, the heating temperature is 53 ~57℃;
[0027] Step S2, heating and fully mixing the initiator, anti-aging agent and flame retardant with the mixture in step S1, the heating temperature is 60-64°C;
[0028] In step S3, the mixture in step S2 is added to a ...
Embodiment 2
[0029] Example 2: Preparation of ethylene propylene rubber
[0030] The proportion of raw materials by weight:
[0031] EPDM rubber, 80 parts; acrylic acid, 4 parts; p-aminobenzenesulfonic acid, 1 part; ammonium persulfate, 1 part; mercaptopropionic acid, 0.6 parts; phenyl-β-naphthylamine, 0.4 parts; initiator , 1 part; anti-aging agent, 2 parts; flame retardant, 1 part; a total of 0.4 parts of benzotriazole and sulfurized isobutylene; the weight ratio of the benzotriazole and sulfurized isobutylene is 3:1.
[0032] Preparation:
[0033] Step S1, heating and premixing EPDM rubber, acrylic acid, p-aminobenzenesulfonic acid, ammonium persulfate, mercaptopropionic acid, phenyl-β-naphthylamine, benzotriazole and vulcanized isobutylene, the heating temperature is 53 ~57℃;
[0034] Step S2, heating and fully mixing the initiator, anti-aging agent and flame retardant with the mixture in step S1, the heating temperature is 60-64°C;
[0035] In step S3, the mixture in step S2 is added to a twin...
Embodiment 3
[0036] Example 3: Preparation of ethylene propylene rubber
[0037] The proportion of raw materials by weight:
[0038] EPDM rubber, 100 parts; acrylic acid, 6 parts; p-aminobenzenesulfonic acid, 3 parts; ammonium persulfate, 2 parts; mercaptopropionic acid, 0.8 parts; phenyl-β-naphthylamine, 0.6 parts; initiator , 3 parts; anti-aging agent, 4 parts; flame retardant, 2 parts; a total of 0.6 parts of benzotriazole and sulfurized isobutylene; the weight ratio of the benzotriazole and sulfurized isobutylene is 5:1.
[0039] Preparation:
[0040] Step S1, heating and premixing EPDM rubber, acrylic acid, p-aminobenzenesulfonic acid, ammonium persulfate, mercaptopropionic acid, phenyl-β-naphthylamine, benzotriazole and vulcanized isobutylene, the heating temperature is 53 ~57℃;
[0041] Step S2, heating and fully mixing the initiator, anti-aging agent and flame retardant with the mixture in step S1, the heating temperature is 60-64°C;
[0042] In step S3, the mixture in step S2 is added to a...
PUM
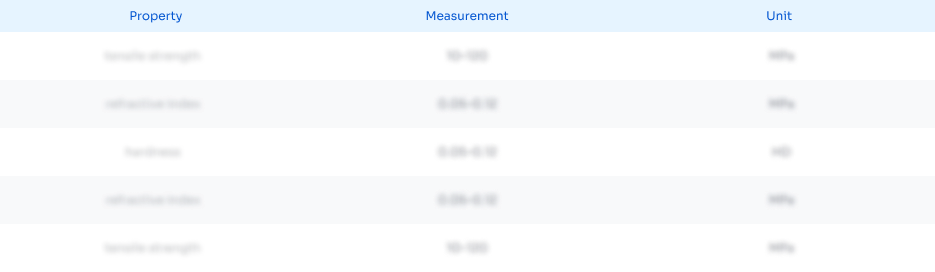
Abstract
Description
Claims
Application Information

- R&D Engineer
- R&D Manager
- IP Professional
- Industry Leading Data Capabilities
- Powerful AI technology
- Patent DNA Extraction
Browse by: Latest US Patents, China's latest patents, Technical Efficacy Thesaurus, Application Domain, Technology Topic, Popular Technical Reports.
© 2024 PatSnap. All rights reserved.Legal|Privacy policy|Modern Slavery Act Transparency Statement|Sitemap|About US| Contact US: help@patsnap.com