Method for recognizing loads of industrial robot
An industrial robot and identification method technology, applied in the field of industrial robot load identification, can solve problems such as long adjustment time, and achieve the effects of ensuring acceleration and solving excessive adjustment time.
- Summary
- Abstract
- Description
- Claims
- Application Information
AI Technical Summary
Problems solved by technology
Method used
Image
Examples
Embodiment Construction
[0015] The technical solutions of the present invention will be described in detail below in conjunction with the accompanying drawings and specific embodiments.
[0016] Such as figure 1 As shown, it is a flow chart of an industrial robot load identification method of the present invention, and the specific steps are:
[0017] S10: Input the dynamics module into the robot control, and solve the real-time torque value.
[0018] Specifically, by applying the dynamic equation of the industrial robot, the dynamic module is input into the robot controller. The real-time torque value is obtained through the angle and angular velocity variation of each joint during the robot's completion of the task. The overall kinetic formula is as follows:
[0019] [ f i τ j ] = I j A ξ ...
PUM
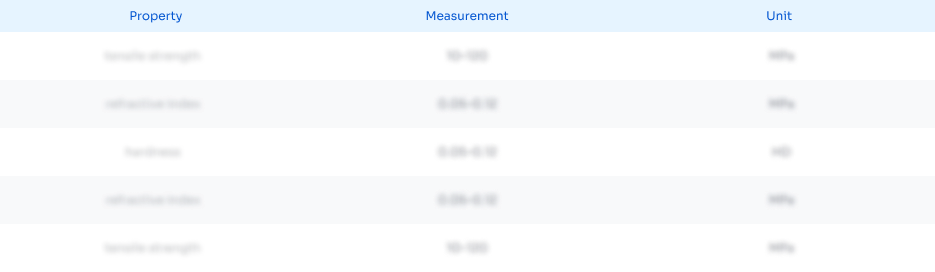
Abstract
Description
Claims
Application Information

- R&D
- Intellectual Property
- Life Sciences
- Materials
- Tech Scout
- Unparalleled Data Quality
- Higher Quality Content
- 60% Fewer Hallucinations
Browse by: Latest US Patents, China's latest patents, Technical Efficacy Thesaurus, Application Domain, Technology Topic, Popular Technical Reports.
© 2025 PatSnap. All rights reserved.Legal|Privacy policy|Modern Slavery Act Transparency Statement|Sitemap|About US| Contact US: help@patsnap.com