Production technology of fire-resistant power cable
A production process and power cord technology, applied in the direction of insulated cables, cable/conductor manufacturing, cables, etc., can solve the problems of fire safety hazards, harmful gas smoke, unsuitable power cords, etc., and achieve excellent electrical transmission performance and high oxygen index , Strong mechanical tensile properties
- Summary
- Abstract
- Description
- Claims
- Application Information
AI Technical Summary
Problems solved by technology
Method used
Examples
Embodiment Construction
[0017] In order to deepen the understanding and recognition of the present invention, the present invention will be further described and introduced below.
[0018] A production process for fire-resistant power cables, (1) using a wire drawing machine to draw copper wires as the conductive cores of the power cables, and sequentially transport the drawn copper wires to an annealing furnace and a copper softening tank for processing;
[0019] (2) The softened copper wire is overlapped and wrapped with two layers of mica tape by a mica tape wrapping machine, and the overlapping rate is controlled at 50%, and the wrapping angle is controlled at 45-50°; the mica tape is made of glass fiber It is made of double-sided coating of low-smoke halogen-free flame-retardant adhesive. The low-smoke halogen-free flame-retardant adhesive is made of 100 parts by weight of acrylic emulsion, 75 parts by weight of aluminum oxalate, and 2 parts by weight sodium hydroxymethylcellulose, 23 parts by w...
PUM
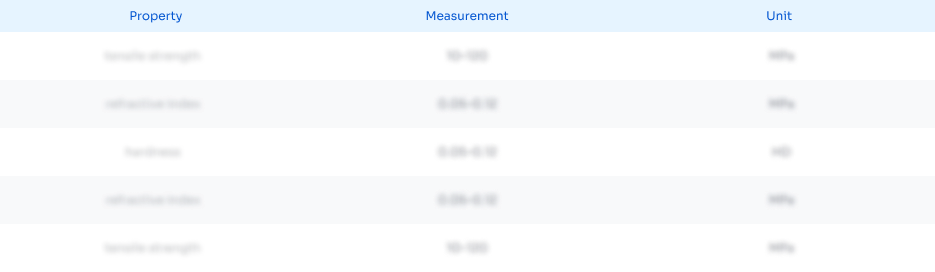
Abstract
Description
Claims
Application Information

- R&D
- Intellectual Property
- Life Sciences
- Materials
- Tech Scout
- Unparalleled Data Quality
- Higher Quality Content
- 60% Fewer Hallucinations
Browse by: Latest US Patents, China's latest patents, Technical Efficacy Thesaurus, Application Domain, Technology Topic, Popular Technical Reports.
© 2025 PatSnap. All rights reserved.Legal|Privacy policy|Modern Slavery Act Transparency Statement|Sitemap|About US| Contact US: help@patsnap.com