Reactant gas delivery device and chemical vapor deposition or epitaxial layer growth reactor
A technology of chemical vapor deposition and conveying device, which is applied in gaseous chemical plating, coating, metal material coating technology and other directions, can solve the problems of poor sealing effect, water leakage, and increase the difficulty of processing and manufacturing.
- Summary
- Abstract
- Description
- Claims
- Application Information
AI Technical Summary
Problems solved by technology
Method used
Image
Examples
Embodiment Construction
[0047] figure 1 A front view cross-sectional schematic view of a reactor provided according to an embodiment of the present invention is shown. The reactor may be used for chemical vapor deposition or epitaxial layer growth, but it should be understood that it is not limited to such applications.
[0048] The reactor 10 includes an outer wall 11 and a top wall 12 surrounding the reaction chamber. At least one substrate carrier 15 and a support device 16 for supporting the substrate carrier 15 are arranged in the reactor 10. In the deposition or epitaxial layer growth reactor, the support device 16 can drive the substrate carrier 15 to rotate, so as to realize the smooth progress of the deposition process or the epitaxial layer growth process. Above the substrate carrier 15 and below the top wall 12, a reaction gas delivery device 100 is arranged, and the reaction gas delivery device 100 is used to deliver at least two groups of different reaction gases to the processing area ...
PUM
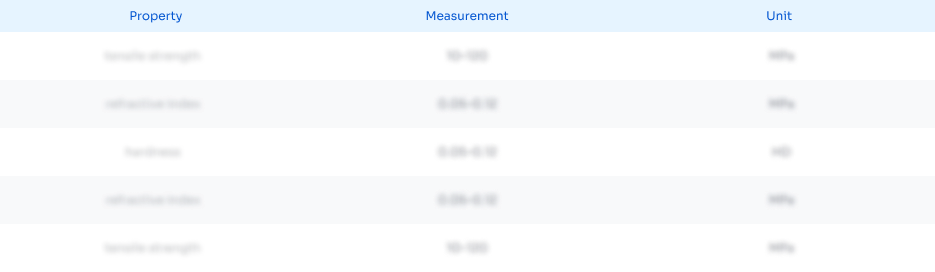
Abstract
Description
Claims
Application Information

- Generate Ideas
- Intellectual Property
- Life Sciences
- Materials
- Tech Scout
- Unparalleled Data Quality
- Higher Quality Content
- 60% Fewer Hallucinations
Browse by: Latest US Patents, China's latest patents, Technical Efficacy Thesaurus, Application Domain, Technology Topic, Popular Technical Reports.
© 2025 PatSnap. All rights reserved.Legal|Privacy policy|Modern Slavery Act Transparency Statement|Sitemap|About US| Contact US: help@patsnap.com