A plasma-crosslinking compound modified high-precision cashmere digital printing process
A plasma and digital printing technology, used in dyeing, textiles and papermaking, etc., can solve the problems of depth less than 10μm, and some processing thicknesses are only about 10 nanometers, achieving strong layering, improved fiber strength, and low energy consumption Effect
- Summary
- Abstract
- Description
- Claims
- Application Information
AI Technical Summary
Problems solved by technology
Method used
Examples
specific Embodiment 1
[0019] A plasma-crosslinking composite modified high-precision cashmere digital printing process, comprising the following steps:
[0020] (1) Cashmere fabric by steaming process: the cashmere fabric is in a loose state, sprayed with 0.3g / L antistatic agent SN, and the fiber weight gain is 100g / m 2 , the fabric is steamed in a J-type steamer at 20 m / min, and steamed at 100 °C with steam or hot air as the medium;
[0021] When the cashmere fabric is in a loose state, the antistatic agent is sprayed and steamed to improve the wetting performance of the cashmere fiber and soften the scale layer structure on the surface of the cashmere fiber, which is beneficial to the subsequent plasma etching and improves the etching effect.
[0022] (2) Plasma etching process of cashmere fabric: AtomfloTM250 atmospheric pressure plasma jet equipment is used to form a plasma jet to modify cashmere fabric. The processing conditions are as follows: medium air, power supply parameters 380V, freque...
specific Embodiment 2
[0030] A plasma-crosslinking composite modified high-precision cashmere digital printing process, comprising the following steps:
[0031] (1) Cashmere fabric by steaming process: the cashmere fabric is in a loose state, sprayed with 0.5g / L antistatic agent SN, and the fiber weight gain is 100g / m 2 , the fabric is steamed in a J-type steamer at 40 m / min, and steamed at 110°C with steam or hot air as the medium;
[0032] When the cashmere fabric is in a loose state, the antistatic agent is sprayed and steamed to improve the wetting performance of the cashmere fiber and soften the scale layer structure on the surface of the cashmere fiber, which is beneficial to the subsequent plasma etching and improves the etching effect.
[0033] (2) Plasma etching process of cashmere fabric: AtomfloTM250 atmospheric pressure plasma jet equipment is used to form a plasma jet to modify cashmere fabric. The processing conditions are as follows: medium air, power supply parameters 380V, frequen...
specific Embodiment 3
[0041] A plasma-crosslinking composite modified high-precision cashmere digital printing process, comprising the following steps:
[0042] (1) Cashmere fabric by steaming process: the cashmere fabric is in a loose state, sprayed with 0.4g / L antistatic agent SN, and the fiber weight gain is 100g / m 2 , the fabric is steamed in a J-type steamer at 30 m / min, and steamed at 105°C with steam or hot air as the medium;
[0043] When the cashmere fabric is in a loose state, the antistatic agent is sprayed and steamed to improve the wetting performance of the cashmere fiber and soften the scale layer structure on the surface of the cashmere fiber, which is beneficial to the subsequent plasma etching and improves the etching effect.
[0044] (2) Plasma etching process of cashmere fabric: AtomfloTM250 atmospheric pressure plasma jet equipment is used to form a plasma jet to modify cashmere fabric. The processing conditions are as follows: medium air, power supply parameters 380V, frequen...
PUM
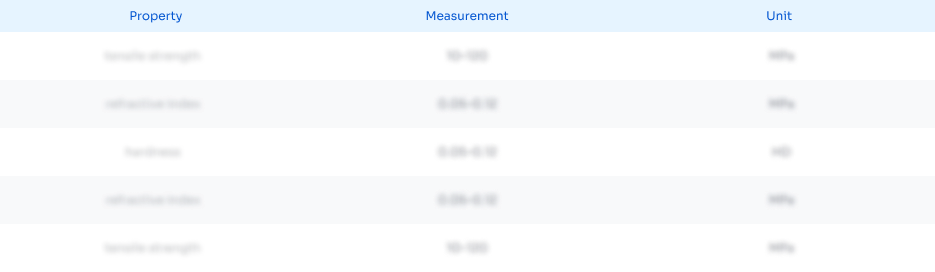
Abstract
Description
Claims
Application Information

- R&D Engineer
- R&D Manager
- IP Professional
- Industry Leading Data Capabilities
- Powerful AI technology
- Patent DNA Extraction
Browse by: Latest US Patents, China's latest patents, Technical Efficacy Thesaurus, Application Domain, Technology Topic, Popular Technical Reports.
© 2024 PatSnap. All rights reserved.Legal|Privacy policy|Modern Slavery Act Transparency Statement|Sitemap|About US| Contact US: help@patsnap.com