A flexible fish-finned double collaborative robot
A robot and robot arm technology, applied in the field of robotics, can solve the problems of immature application of the internal motion principle of fish fins, etc., and achieve the effect of light weight, flexible controllability, and small inertia
- Summary
- Abstract
- Description
- Claims
- Application Information
AI Technical Summary
Problems solved by technology
Method used
Image
Examples
Embodiment Construction
[0028] Below in conjunction with accompanying drawing, preferred embodiment of the present invention is described in detail:
[0029] Such as figure 1 As shown, a flexible imitation fin double collaborative robot includes a machine frame 1, a robot arm module a2 and a robot arm module b3, and is characterized in that: the robot arm module a2 and the robot arm module b3 are installed horizontally and vertically on the machine On the table frame 1, the maximum efficient cooperation of the arms is realized.
[0030] The robot arm module b3 includes a power module 4, a mechanical arm module 5 and a mechanical wrist module 6. The power module 4 is respectively fixed on the machine frame 1 by screws, and one end of the mechanical arm module 5 is fixed on the power module by a set screw. 4, the other end is screwed to the mechanical wrist module 6; the robot arm module a2 has the same structure as the robot arm module b3. The movement process is as follows: install the mechanical g...
PUM
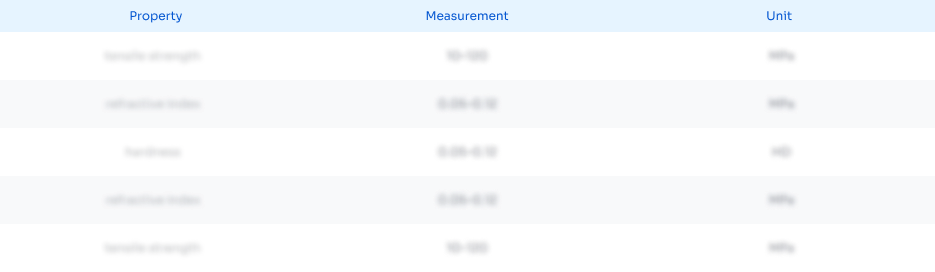
Abstract
Description
Claims
Application Information

- R&D
- Intellectual Property
- Life Sciences
- Materials
- Tech Scout
- Unparalleled Data Quality
- Higher Quality Content
- 60% Fewer Hallucinations
Browse by: Latest US Patents, China's latest patents, Technical Efficacy Thesaurus, Application Domain, Technology Topic, Popular Technical Reports.
© 2025 PatSnap. All rights reserved.Legal|Privacy policy|Modern Slavery Act Transparency Statement|Sitemap|About US| Contact US: help@patsnap.com