Fault diagnosis method and apparatus for rolling bearing
A technology for rolling bearings and faults, which is applied in the field of fault diagnosis of rolling bearings. It can solve the problems of not being able to get rid of hardware, extraction, and features that cannot be realized in early faults, so as to avoid the interference of human factors and improve the accuracy.
- Summary
- Abstract
- Description
- Claims
- Application Information
AI Technical Summary
Problems solved by technology
Method used
Image
Examples
Embodiment 1
[0023] figure 1 It is a schematic flow chart of the rolling bearing fault diagnosis method in Embodiment 1 of the present invention, such as figure 1 As shown, the fault diagnosis methods of rolling bearings include:
[0024] Step 110: Collect the vibration signal of the rolling bearing, and obtain the time-frequency spectrum of the vibration signal.
[0025] In a specific implementation manner, an acceleration sensor may be installed at the measuring position on the rolling bearing seat, and the vibration signal of the rolling bearing may be collected through the provided acceleration sensor. figure 2 is the waveform diagram of the simulated vibration signal of the rolling bearing, the simulated vibration signal is expressed by the following formula (1), where t is the time and X(t) is the amplitude:
[0026] X(t)=(1+sin(4πt 2 ))×sin(332πt 2 )………………………………………Formula 1)
[0027] One of the following methods can be used to obtain the time-frequency spectrum of the vibratio...
Embodiment 2
[0072] Figure 12 It is a schematic structural diagram of a rolling bearing fault diagnosis device according to Embodiment 2 of the present invention. It can be used to execute the steps of the method for diagnosing the rolling bearing in Embodiment 1 of the present invention.
[0073] refer to Figure 12 , the rolling bearing fault diagnosis device includes a signal acquisition and spectrum acquisition module 1210 , an order component determination module 1220 , an angle resampling module 1230 and a fault diagnosis module 1240 .
[0074] The signal collection module 1210 is used to collect the vibration signal of the rolling bearing, and obtain the time-frequency spectrum of the vibration signal.
[0075] The order component determination module 1220 is used to determine the optimal order component of the vibration signal according to the time-frequency spectrum.
[0076] Specifically, the order component determination module 1220 includes:
[0077] The conversion frequen...
PUM
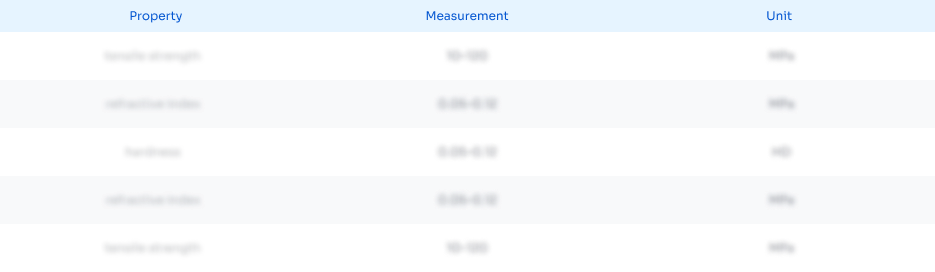
Abstract
Description
Claims
Application Information

- R&D
- Intellectual Property
- Life Sciences
- Materials
- Tech Scout
- Unparalleled Data Quality
- Higher Quality Content
- 60% Fewer Hallucinations
Browse by: Latest US Patents, China's latest patents, Technical Efficacy Thesaurus, Application Domain, Technology Topic, Popular Technical Reports.
© 2025 PatSnap. All rights reserved.Legal|Privacy policy|Modern Slavery Act Transparency Statement|Sitemap|About US| Contact US: help@patsnap.com