Special equipment for large cylinder butt milling and welding
A large cylinder and special equipment technology, applied in other manufacturing equipment/tools, manufacturing tools, etc., can solve the problems of heavy smoke and dust, operator bodily injury, frequent cylinder hoisting, high labor intensity, etc., to reduce the impact of dust and high temperature on the human body damage, a high pass rate of one-time molding, and the effect of reducing potential safety hazards
- Summary
- Abstract
- Description
- Claims
- Application Information
AI Technical Summary
Problems solved by technology
Method used
Image
Examples
Embodiment Construction
[0017] The specific implementation manners of the present invention will be described in further detail below with reference to the accompanying drawings.
[0018] Such as figure 1 and 2 The special equipment for butt milling and welding of large cylinders shown includes no less than two cylinder rolling frames 12, a guide rail 11 is provided under the cylinder rolling frames 12, and a pair of 360-degree rotating edge milling machines are provided at the left end of the guide rails 11. A pair of The 360-degree rotary edge milling machine includes a 360-degree rotary edge milling machine 27 at the left end and a 360-degree rotary edge milling machine 23 at the right end. 23 is arranged on the guide rail 11, a V-shaped bracket is arranged between the two 360-degree rotating edge milling machines, a ratchet device 7 is arranged on the V-shaped bracket, the ratchet device 7 is connected with a belt 8, and the right end side of the guide rail 11 is fixed with a Welding device, cy...
PUM
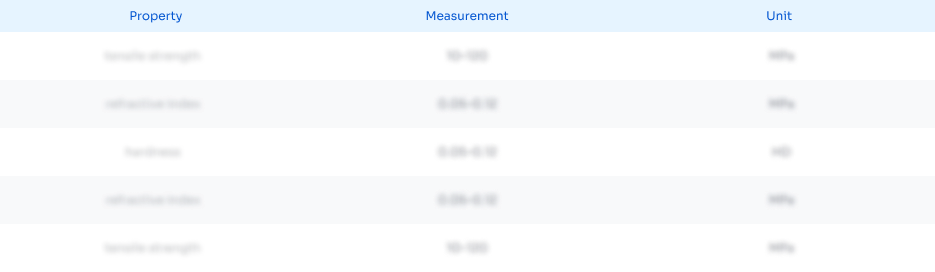
Abstract
Description
Claims
Application Information

- R&D
- Intellectual Property
- Life Sciences
- Materials
- Tech Scout
- Unparalleled Data Quality
- Higher Quality Content
- 60% Fewer Hallucinations
Browse by: Latest US Patents, China's latest patents, Technical Efficacy Thesaurus, Application Domain, Technology Topic, Popular Technical Reports.
© 2025 PatSnap. All rights reserved.Legal|Privacy policy|Modern Slavery Act Transparency Statement|Sitemap|About US| Contact US: help@patsnap.com