Stamping forming process and trimming and shaping composite mould for automobile roof cover
A technology for automobile top cover and stamping forming, which is applied to forming tools, manufacturing tools, vehicle parts, etc., can solve the problems of inaccurate positioning, poor stability and production consistency, and increased number of mold processes, so as to reduce the cost of mold tooling, Avoid the effect of scrap that cannot fall off and the number of mold processes
- Summary
- Abstract
- Description
- Claims
- Application Information
AI Technical Summary
Problems solved by technology
Method used
Image
Examples
Embodiment Construction
[0043] refer to figure 1, the trimming and shaping compound mold that is used for automobile roof of the present embodiment comprises upper mold base, lower mold base 11, trimming punch 12, trimming die 21, shaping insert 4, top pressing core 31, top Nitrogen spring 32, etc., wherein the trimming punch 12 is installed on the lower die base 11, the trimming die 21, the shaping insert 4, the top pressing core 31 are installed on the upper die base, and the top nitrogen spring 32 is installed on the upper die base Between the top pressing core 31. For clarity, figure 1 In the middle, the upper mold base is omitted. The top pressing core 31 is used for pressing the top of the car roof during stamping, and the top nitrogen spring 32 acts on the top pressing core 31 to provide top pressing force.
[0044] refer to figure 2 , the tail pressing core 51 is used for the tail pressing of the car roof, and the tail nitrogen spring 52 acts on the tail pressing core 51 to provide the t...
PUM
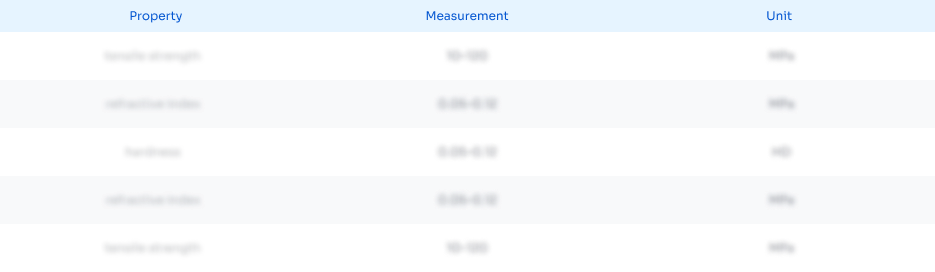
Abstract
Description
Claims
Application Information

- R&D
- Intellectual Property
- Life Sciences
- Materials
- Tech Scout
- Unparalleled Data Quality
- Higher Quality Content
- 60% Fewer Hallucinations
Browse by: Latest US Patents, China's latest patents, Technical Efficacy Thesaurus, Application Domain, Technology Topic, Popular Technical Reports.
© 2025 PatSnap. All rights reserved.Legal|Privacy policy|Modern Slavery Act Transparency Statement|Sitemap|About US| Contact US: help@patsnap.com