Machining process for metal pipes with punched holes
A processing technology, metal pipe technology, applied in the field of metal pipe processing, can solve the problems of increased transportation volume, increased mold occupation requirements, increased labor costs, etc., to achieve the effects of improving production efficiency, improving processing efficiency, and saving labor costs
- Summary
- Abstract
- Description
- Claims
- Application Information
AI Technical Summary
Problems solved by technology
Method used
Image
Examples
Embodiment Construction
[0015] The present invention will be further described below in conjunction with specific embodiments.
[0016] The metal pipe processing technology with punching of the present invention includes a blanking tool and a punching tool, and also includes a positioning mechanism for determining the length of the blanking. See figure 1 with figure 2 , The punching tooling includes a work platform 1, and four corners of the bottom surface of the work platform 1 are provided with support legs 2; on the upper surface of the work platform 1 (through a pad) is provided with a vertical support plate 3, the support plate 3 along the middle position of the height A horizontal pipe sleeve core column 4 is provided, and a horizontal connecting horizontal plate 5 is provided at the upper end of the supporting plate 3. The connecting horizontal plate 5 and the casing core column 4 are located on the same side of the supporting plate 3. Two vertically upward and parallel cam connecting blocks 6 ...
PUM
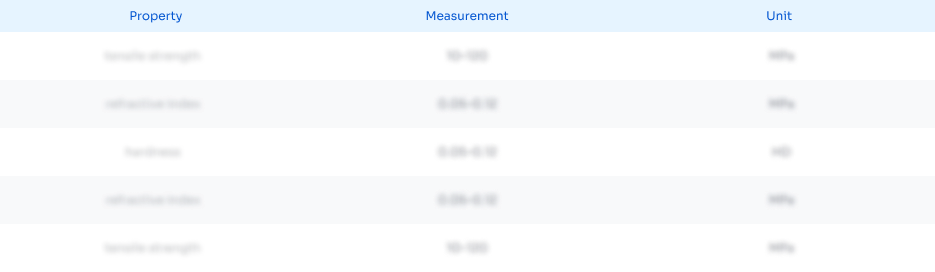
Abstract
Description
Claims
Application Information

- Generate Ideas
- Intellectual Property
- Life Sciences
- Materials
- Tech Scout
- Unparalleled Data Quality
- Higher Quality Content
- 60% Fewer Hallucinations
Browse by: Latest US Patents, China's latest patents, Technical Efficacy Thesaurus, Application Domain, Technology Topic, Popular Technical Reports.
© 2025 PatSnap. All rights reserved.Legal|Privacy policy|Modern Slavery Act Transparency Statement|Sitemap|About US| Contact US: help@patsnap.com