Motor iron core molding die
A technology for forming molds and iron cores, which is used in the manufacture of stator/rotor bodies, etc., and can solve the problems of low concentricity of silicon steel sheets, reduced machining accuracy of motor iron cores, and uneven force on the rotor seat.
- Summary
- Abstract
- Description
- Claims
- Application Information
AI Technical Summary
Problems solved by technology
Method used
Image
Examples
Embodiment Construction
[0010] See figure 1 , figure 2 , a motor core forming die, which includes a stamping forming device 1, a superimposed stamping forming device 2 and a waste cutting device 3, the superimposing stamping forming device 2 includes a punching rotor stacking die head 4 and a rotor seat 5, and a punching rotor stacking die The head 4 is set on the upper mold 6, the rotor base 5 is set on the lower mold 7, the rotor base 5 is set with a needle roller sleeve 8, the rotor base 5 is connected to the servo motor 10 through the belt 9, and the rotation angle of the rotor base is controlled by the servo motor. Make the stacking riveting force evenly act on the iron core and not concentrate on one point, thereby reducing the cumulative error of the stacking of silicon steel sheets, improving the parallelism, verticality and concentricity of the product, and effectively reducing the noise of the motor. The service life of the motor is improved, while the wear of the rotor seat is reduced, a...
PUM
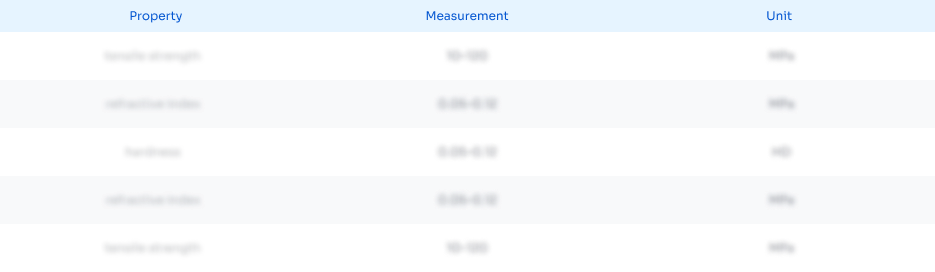
Abstract
Description
Claims
Application Information

- R&D
- Intellectual Property
- Life Sciences
- Materials
- Tech Scout
- Unparalleled Data Quality
- Higher Quality Content
- 60% Fewer Hallucinations
Browse by: Latest US Patents, China's latest patents, Technical Efficacy Thesaurus, Application Domain, Technology Topic, Popular Technical Reports.
© 2025 PatSnap. All rights reserved.Legal|Privacy policy|Modern Slavery Act Transparency Statement|Sitemap|About US| Contact US: help@patsnap.com