An internal riveting die for hydraulic clutch bearing gland
A clutch bearing and riveting technology, which is applied in the direction of forming tools, manufacturing tools, metal processing equipment, etc., can solve the problems of waste of materials, long time consumption of molds, unfavorable mold management, etc.
- Summary
- Abstract
- Description
- Claims
- Application Information
AI Technical Summary
Problems solved by technology
Method used
Image
Examples
Embodiment
[0028] When it is necessary to rivet the inner hydraulic cover of the hydraulic bearing, first install the mold on the press, install the bottom plate 1 on the press table, and install the lower fixing plate 2 and the lower mold fixing plate 3 through the fixing screws 4 On the bottom plate, select an appropriate split-type lower die insert 10 according to the model of the hydraulic bearing, and install the split-type lower die insert 10 in the lower die fixing plate 3. At the same time, in order to ensure that the split-type lower die insert 10 works More stable, the lower mold cover plate 11 covering the split type lower mold insert 10 is installed on the upper end of the split type lower mold insert 10, and then the lower fixing plate 5 equipped with the connecting plate 6 is passed through the mold handle on the connecting plate 6 The protrusion is connected with the pressure head of the press, and the mandrel 8 is installed in the middle of the lower end face of the lower ...
PUM
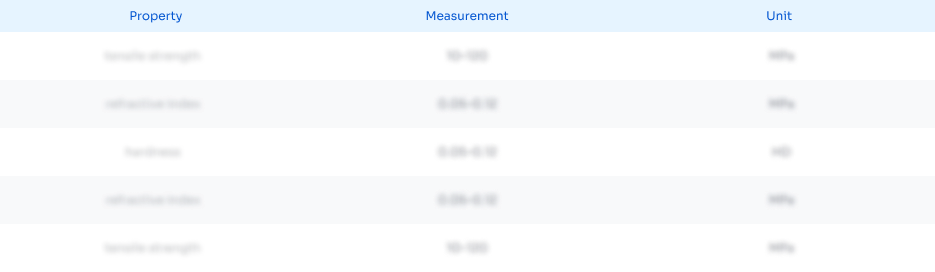
Abstract
Description
Claims
Application Information

- R&D
- Intellectual Property
- Life Sciences
- Materials
- Tech Scout
- Unparalleled Data Quality
- Higher Quality Content
- 60% Fewer Hallucinations
Browse by: Latest US Patents, China's latest patents, Technical Efficacy Thesaurus, Application Domain, Technology Topic, Popular Technical Reports.
© 2025 PatSnap. All rights reserved.Legal|Privacy policy|Modern Slavery Act Transparency Statement|Sitemap|About US| Contact US: help@patsnap.com