A Thermal Parameter Recognition Method Based on Affine Transformation Best Matching Image
A technology of thermal parameters and affine transformation, applied in the direction of thermal expansion coefficient of materials, testing the strength of materials by applying a stable bending force, etc. It can solve the problems of time-consuming and complicated calculation process, and achieve easy operation, eliminate errors, and reduce repetition. The effect of heating costs
- Summary
- Abstract
- Description
- Claims
- Application Information
AI Technical Summary
Problems solved by technology
Method used
Image
Examples
Embodiment 1
[0056] see figure 1 Shown is a specific embodiment of a thermal parameter identification method based on an affine transformation best matching image described in this application. The method described in this embodiment includes the following steps:
[0057] Step 101, making a high-temperature speckle test piece, fixing the prepared high-temperature speckle test piece on a three-point bending testing machine with a high-temperature box, and collecting a speckle image a of the test piece before deformation;
[0058] Step 102, apply a thermal load, and collect the deformed speckle image b of the test piece;
[0059] Step 103, select a calibration area on the speckle image a before deformation, and complete the calibration of the actual length of the unit pixel;
[0060] Step 104. Select the calculation area on the speckle image a before deformation, take the thermal parameter to be measured as the quantity to be optimized, and set the iteration initial value p 0 :
[0061] p...
Embodiment 3
[0122] figure 2 Best fit image model for affine transformation. Use monochromatic light illumination and acquisition device to collect speckle image 1 before deformation (image a), apply thermal load, unknown material parameters 2 control thermal load deformation 3, and form deformed image 4 (image b). According to the thermal parameters to be optimized, the initial value of iteration is assumed to be 5. The affine transformation 6 is completed according to the iterative initial value, and an undeformed image 7 (image c) is obtained. Using the optimization iterative algorithm to construct the pre-deformed image, that is, construct the undeformed image 7 (image c) and the pre-deformed image 1 (image a), perform iterative optimization 8, and output the measurement results of thermal parameters 10 when the best matching 9 is achieved.
[0123] image 3 It is the schematic diagram of affine transformation. The affine transformation displacement is composed of rigid body trans...
PUM
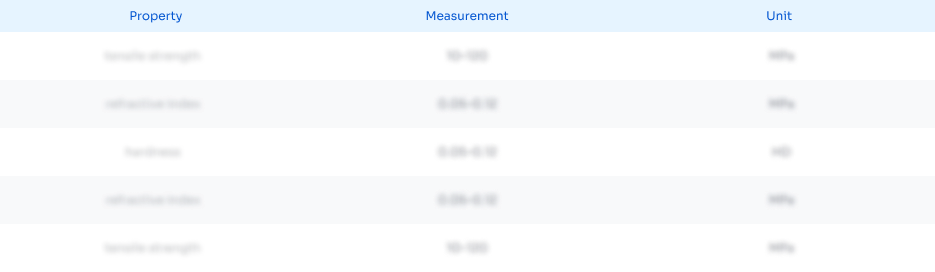
Abstract
Description
Claims
Application Information

- R&D
- Intellectual Property
- Life Sciences
- Materials
- Tech Scout
- Unparalleled Data Quality
- Higher Quality Content
- 60% Fewer Hallucinations
Browse by: Latest US Patents, China's latest patents, Technical Efficacy Thesaurus, Application Domain, Technology Topic, Popular Technical Reports.
© 2025 PatSnap. All rights reserved.Legal|Privacy policy|Modern Slavery Act Transparency Statement|Sitemap|About US| Contact US: help@patsnap.com