Face gear and herringbone-tooth cylindrical gear combined four-way branch transmission mechanism
A technology of cylindrical gear and herringbone gear, which is applied in the field of four-way branch transmission mechanism, can solve the problems of limited use and inability to realize the reversing function, and achieve the effects of weight reduction, compact structure and strong bearing capacity
- Summary
- Abstract
- Description
- Claims
- Application Information
AI Technical Summary
Problems solved by technology
Method used
Image
Examples
Embodiment Construction
[0019] Below in conjunction with accompanying drawing this design is described in detail:
[0020] Such as figure 1 As shown, the present invention includes a first power input shaft 1, and the first power input shaft 1 is connected to the first helical spur gear 3 through a first overrunning clutch 2; the first helical spur gear 3 is connected to the first upper surface The gear 4a and the second lower gear 4b mesh up and down at the same time; the above-mentioned first helical cylindrical gear 3 adopts radial floating support; the above-mentioned first upper gear 4a is connected to the first herringbone cylindrical gear 8a through the first transmission shaft 5a; the above-mentioned The second lower gear 4b is connected to the second herringbone cylindrical gear 8b through the second transmission shaft 5b; the above-mentioned first herringbone cylindrical gear 8a is connected with the third herringbone cylindrical gear 7a and the fourth herringbone cylindrical gear 7b simult...
PUM
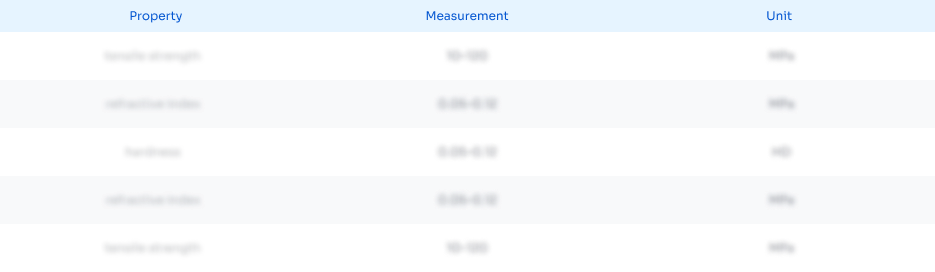
Abstract
Description
Claims
Application Information

- R&D
- Intellectual Property
- Life Sciences
- Materials
- Tech Scout
- Unparalleled Data Quality
- Higher Quality Content
- 60% Fewer Hallucinations
Browse by: Latest US Patents, China's latest patents, Technical Efficacy Thesaurus, Application Domain, Technology Topic, Popular Technical Reports.
© 2025 PatSnap. All rights reserved.Legal|Privacy policy|Modern Slavery Act Transparency Statement|Sitemap|About US| Contact US: help@patsnap.com