A mixed-material lignite drying and upgrading method and the device used therein
A technology of drying device and mixing device, which is applied in the direction of drying solid materials, heating to dry solid materials, drying, etc., can solve the problems of increasing transportation costs, increasing equipment investment, increasing production costs, etc., and achieve energy consumption and production costs Low cost, low investment cost, moisture reduction effect
- Summary
- Abstract
- Description
- Claims
- Application Information
AI Technical Summary
Problems solved by technology
Method used
Image
Examples
Embodiment 1
[0021] The lignite raw coal is crushed by the crushing device 1, and the crushed lignite raw coal is sent to the screening device 2 for screening, and the lump coal with a particle size of 5-8 mm or more screened by the screening device 2 is sent to the drying device 3 for drying. The temperature in the drying device 3 is 150°C, and the material stays in the drying device 3 for 60 minutes, so that the moisture in the lignite is reduced to below 8%, and the temperature of the dried lignite reaches 110°C. At this time, the calorific value of the dried lignite can be increased to More than 5000Kcal / kg; the dried hot lignite is sent to the cooling device 4, and heat transfer occurs with the cooling medium in the cooling device 4, so that the temperature of the dried lignite is reduced to 40°C. The cooling medium is cold air or inert Gas; the dry lignite is sent into the mixing device 5 after being initially cooled by the above-mentioned cooling device 4, and in the mixing device 5,...
Embodiment 2
[0023] The lignite raw coal is crushed by the crushing device 1, and the crushed lignite raw coal is sent to the screening device 2 for screening, and the lump coal with a particle size of 5-8 mm or more screened by the screening device 2 is sent to the drying device 3 for drying. The temperature in the drying device 3 is 350°C, and the material stays in the drying device 3 for 20 minutes, so that the moisture in the lignite is reduced to below 5%, and the temperature of the dried lignite reaches 150°C. At this time, the calorific value of the dried lignite can be increased to More than 5000Kcal / kg; the dried hot lignite is sent to the cooling device 4, and heat transfer occurs with the cooling medium in the cooling device 4, so that the temperature of the dried lignite is reduced to 80°C. The cooling medium is cold air or inert Gas; the dry lignite is sent into the mixing device 5 after being initially cooled by the above-mentioned cooling device 4, and in the mixing device 5,...
Embodiment 3
[0025] The lignite raw coal is crushed by the crushing device 1, and the crushed lignite raw coal is sent to the screening device 2 for screening, and the lump coal with a particle size of 5-8 mm or more screened by the screening device 2 is sent to the drying device 3 for drying. The temperature in the drying device 3 is 250°C, and the material stays in the drying device 3 for 40 minutes, so that the moisture in the lignite is reduced to below 10%, and the temperature of the dried lignite reaches 50°C. At this time, the calorific value of the dried lignite can be increased to More than 5000Kcal / kg; the dried hot lignite is sent to the cooling device 4, and heat transfer occurs with the cooling medium in the cooling device 4, so that the temperature of the dried lignite is reduced to 60°C. The cooling medium is cold air or inert Gas; the dry lignite is sent into the mixing device 5 after being initially cooled by the above-mentioned cooling device 4, and in the mixing device 5,...
PUM
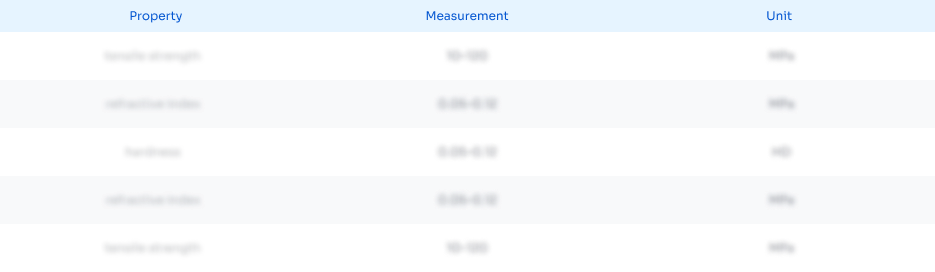
Abstract
Description
Claims
Application Information

- R&D
- Intellectual Property
- Life Sciences
- Materials
- Tech Scout
- Unparalleled Data Quality
- Higher Quality Content
- 60% Fewer Hallucinations
Browse by: Latest US Patents, China's latest patents, Technical Efficacy Thesaurus, Application Domain, Technology Topic, Popular Technical Reports.
© 2025 PatSnap. All rights reserved.Legal|Privacy policy|Modern Slavery Act Transparency Statement|Sitemap|About US| Contact US: help@patsnap.com