MEMS-based conformal air speed sensor
A sensor and pressure sensor technology, applied in the field of sensors, can solve problems such as blockage and pitot tube icing, and achieve the effect of preventing icing, reducing the possibility of icing, and reducing the possibility of blockage
- Summary
- Abstract
- Description
- Claims
- Application Information
AI Technical Summary
Problems solved by technology
Method used
Image
Examples
Embodiment Construction
[0031] For purposes of illustration, embodiments of systems and methods for measuring space velocity using MEMS-based pressure sensors will now be disclosed in detail. However, alternative pressure sensors of suitable size and sensitivity, which are not fabricated using improved semiconductor device fabrication techniques, may be utilized.
[0032]According to embodiments disclosed herein, the system includes an array of MEMS capacitive differential pressure sensors with their associated signal conditioning, and a locally flexible conformal surface structure with input for the MEMS capacitive differential pressure sensors and still air Airways and holes for inhalation. The system further includes a processor that calculates a final airspeed estimate. Preferably, means for heating the conformal surface (to prevent airway icing) are provided. If the conformal surface is made of metal or other thermally conductive material, the heating method may include attaching a resistive h...
PUM
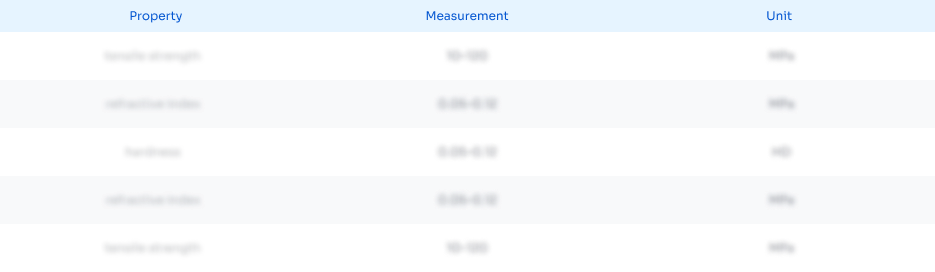
Abstract
Description
Claims
Application Information

- R&D
- Intellectual Property
- Life Sciences
- Materials
- Tech Scout
- Unparalleled Data Quality
- Higher Quality Content
- 60% Fewer Hallucinations
Browse by: Latest US Patents, China's latest patents, Technical Efficacy Thesaurus, Application Domain, Technology Topic, Popular Technical Reports.
© 2025 PatSnap. All rights reserved.Legal|Privacy policy|Modern Slavery Act Transparency Statement|Sitemap|About US| Contact US: help@patsnap.com