Adding method and device of inhibitor used for reducing generation of dioxin in sintering process
A technology of sintering process and adding devices, which is applied in the field of flue gas purification treatment, which can solve the problems of increasing the concentration of nitrogen oxides in the sintering tail gas and increasing operating costs, and achieves the reduction of dioxin generation, reduction of usage, and mixing effect strong effect
- Summary
- Abstract
- Description
- Claims
- Application Information
AI Technical Summary
Problems solved by technology
Method used
Image
Examples
Embodiment 1
[0052] The hourly consumption of mixture in a sintering plant is 899t / h, of which the consumption of sintered pellets is 7t / h. Calculated based on the addition of 0.01% inhibitor, the amount of inhibitor added per hour is 89.9kg, calculated as a solution with a concentration of 20%, then 449.5kg of inhibitor solution needs to be added to the mixture per hour, if the inhibitor solution is directly added Mixed material is equivalent to a proportion of 0.05%. However, using the two-stage mixing method, first mix 449.5kg of inhibitor solution into 7t sintered pellets, which is equivalent to a ratio of 6.4%. Compared with directly mixing into the mixture, the direct amplification is 128 times, which greatly increases the mixing effect of the inhibitor in the sintering mixture. In addition, after adding sintered pellets, the pyrolysis speed of the inhibitor is slowed down, and the inhibitory effect on the formation of dioxin is enhanced. Therefore, under the premise of low proport...
Embodiment 2
[0059] In the present invention, the inhibitor solution can also be added to the sintering mixture through the coke distribution system using the principle of two-stage mixing. as attached figure 2 As shown, after the inhibitor solution is configured as a 20% solution through the inhibitor preparation system, the formula (1) is used to calculate that when the hourly usage of the sinter mixture is 899t / h, the inhibitor addition ratio is 0.01%, Then the additive amount of the inhibitor solution is 0.4495t / h. First, according to this ratio, the inhibitor solution is evenly distributed on the surface of the coke powder, and the first-stage mixing is performed. Then it enters the sintering material mixer together with the coke powder for secondary mixing to form a sintering mixture, which is sent to the sintering machine material bed for sintering process. In this example, according to the ratio of coke powder, the hourly consumption of coke powder is 32.4t / h. The inhibitor solu...
Embodiment 3
[0062] According to the addition mode of embodiment 2, be 450m2 with one sintering area 2 The sintering machine is the implementation object, relative to the sintering mixture, the ratio of the urea solution is 0.005%, 0.0075, 0.01%, respectively, then relative to the coke powder, the ratio of the urea solution is enlarged by 28 times, respectively becomes 0.14%, 0.21%, 0.28%. The experiments were carried out by two-stage addition method. In addition, a comparative test was carried out in which urea solution was added directly to the mix. Experimental results show that in engineering applications, when urea is added in amounts of 0.005%, 0.0075, and 0.01% (wt% sintered mixture), when urea is directly added to the mixture, the removal rates of dioxins are 10%, 21%, respectively. % and 25%, and by the addition method of the present invention, the removal rate of dioxin can reach about 17%, 46% and 52% respectively. It shows that the two-pole addition method is obviously bette...
PUM
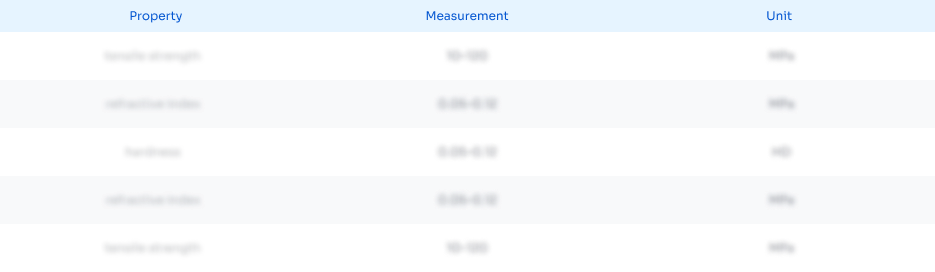
Abstract
Description
Claims
Application Information

- R&D
- Intellectual Property
- Life Sciences
- Materials
- Tech Scout
- Unparalleled Data Quality
- Higher Quality Content
- 60% Fewer Hallucinations
Browse by: Latest US Patents, China's latest patents, Technical Efficacy Thesaurus, Application Domain, Technology Topic, Popular Technical Reports.
© 2025 PatSnap. All rights reserved.Legal|Privacy policy|Modern Slavery Act Transparency Statement|Sitemap|About US| Contact US: help@patsnap.com