A simulation test device for dislocation of weak structural belts under stress
A stress action and simulation test technology, applied in the direction of using mechanical devices, measuring devices, instruments, etc., can solve problems such as large differences, difficulty in simulating three-dimensional stress states, and difficult conclusions to explain problems, so as to avoid uneven radial stress. Effect
- Summary
- Abstract
- Description
- Claims
- Application Information
AI Technical Summary
Problems solved by technology
Method used
Image
Examples
Embodiment Construction
[0032] The principles and features of the present invention are described below in conjunction with the accompanying drawings, and the examples given are only used to explain the present invention, and are not intended to limit the scope of the present invention.
[0033] Such as Figure 1-5 As shown, a kind of simulation test device for the dislocation of weak structural belts under the action of stress includes a base 1 on which a left sample chamber 2, a dislocation chamber 3 and a right sample chamber 4 are sequentially arranged, and the left sample chamber 2 The left sample chamber 2, the shift chamber 3, and the right sample chamber 4 are all rectangular columns, and the three are respectively provided with left through holes for placing samples. 61. The middle through hole 62 and the right through hole 63, the above three through holes are equidiameter cylindrical through holes, sliding the left sample chamber 2 and the shift chamber 3 along the guide rail 5 can make th...
PUM
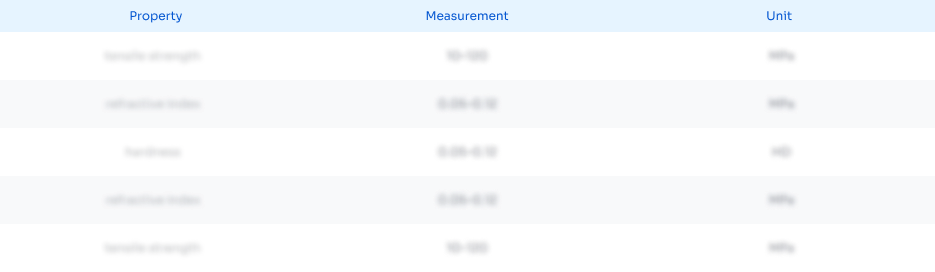
Abstract
Description
Claims
Application Information

- R&D
- Intellectual Property
- Life Sciences
- Materials
- Tech Scout
- Unparalleled Data Quality
- Higher Quality Content
- 60% Fewer Hallucinations
Browse by: Latest US Patents, China's latest patents, Technical Efficacy Thesaurus, Application Domain, Technology Topic, Popular Technical Reports.
© 2025 PatSnap. All rights reserved.Legal|Privacy policy|Modern Slavery Act Transparency Statement|Sitemap|About US| Contact US: help@patsnap.com