A Novel Strong Robust Current Control Method for Brushless DC Motors
A technology of brushed DC motors and DC motors, applied in current controllers, motor generator controls, electronically commutated motor controls, etc., can solve the problem of poor dynamic response of adaptive current control, failure to meet high-performance control requirements, and high-frequency gain Instability and other problems, to avoid high-frequency vibration, good dynamic and static tracking performance, and improve the effect of dynamic tracking ability
- Summary
- Abstract
- Description
- Claims
- Application Information
AI Technical Summary
Problems solved by technology
Method used
Image
Examples
Embodiment Construction
[0040] A novel strong and robust current control method for a brushless DC motor of the present invention will be described in detail below with reference to the embodiments and the accompanying drawings.
[0041] In the novel brushless DC motor strong robust current control method of the present invention, the brushless DC motor adopts a two-phase conduction control mode. The modulation mode of switching tube chopping controls the input voltage of the motor, so as to realize the purpose of controlling the motor current.
[0042] The current control strategy of the whole brushless DC motor in the present invention is as follows figure 1 shown. The control strategy mainly includes speed controller, optimal reference current calculation, current controller and commutation controller. Among them, the optimal reference current calculation and the commutation controller are used to suppress the non-ideal back EMF and the torque fluctuation generated by the commutation process. B...
PUM
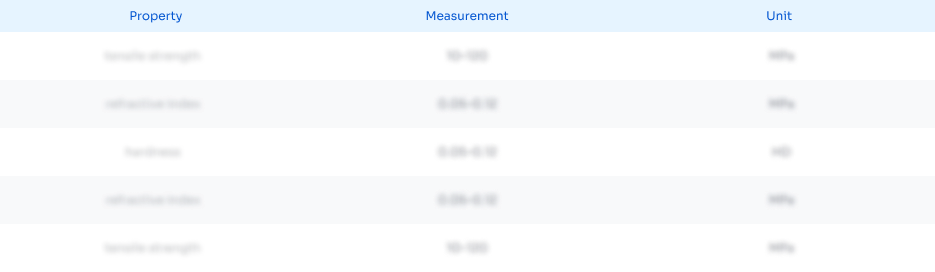
Abstract
Description
Claims
Application Information

- Generate Ideas
- Intellectual Property
- Life Sciences
- Materials
- Tech Scout
- Unparalleled Data Quality
- Higher Quality Content
- 60% Fewer Hallucinations
Browse by: Latest US Patents, China's latest patents, Technical Efficacy Thesaurus, Application Domain, Technology Topic, Popular Technical Reports.
© 2025 PatSnap. All rights reserved.Legal|Privacy policy|Modern Slavery Act Transparency Statement|Sitemap|About US| Contact US: help@patsnap.com