Split flow-guide type aluminum alloy heat dissipating profile
An aluminum alloy and split technology, which is applied in the field of split inductive aluminum alloy heat dissipation profiles, can solve the problems of low heat dissipation efficiency, easy occurrence of wrinkles or cracks in aluminum alloy billets, and inability to form large convection, so as to improve heat dissipation. The effect of efficiency
- Summary
- Abstract
- Description
- Claims
- Application Information
AI Technical Summary
Problems solved by technology
Method used
Image
Examples
Embodiment Construction
[0012] Examples of the present invention figure 1 , 2 As shown, the split diversion aluminum alloy heat dissipation profile includes a main radiator 1 and a secondary radiator 2 made of aluminum alloy extruded by an extruder. The main radiator is composed of a main substrate 3 and a wing plate 4. The main substrate and The wing plates are long strip plates, one side of the main substrate is the heat dissipation connection surface, and the three strict and three solid heat dissipation connection surfaces are connected to the heating electronic components or machines, and the wing plate is connected to the other side of the main substrate opposite to the heat dissipation surface. The board is perpendicular to the connection surface and the longitudinal direction is consistent with the longitudinal direction of the main substrate. There are at least two wing plates. This embodiment is eight. The specific number can be determined according to the specific application environment a...
PUM
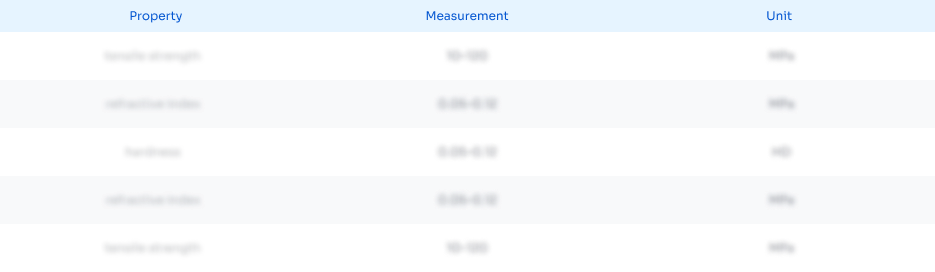
Abstract
Description
Claims
Application Information

- R&D Engineer
- R&D Manager
- IP Professional
- Industry Leading Data Capabilities
- Powerful AI technology
- Patent DNA Extraction
Browse by: Latest US Patents, China's latest patents, Technical Efficacy Thesaurus, Application Domain, Technology Topic, Popular Technical Reports.
© 2024 PatSnap. All rights reserved.Legal|Privacy policy|Modern Slavery Act Transparency Statement|Sitemap|About US| Contact US: help@patsnap.com