Device and method for measuring z-axis vibration displacement
A vibration displacement, Z-axis technology, applied in the direction of measuring devices, instruments, etc., can solve the problems that the measurement method cannot accurately measure the Z-axis displacement of the vehicle, affect the application and promotion of active vibration reduction technology, and lead or lag the phase angle, etc. The effects of mass production and popularization, improved structure compactness and reliability, and good low-frequency response performance
- Summary
- Abstract
- Description
- Claims
- Application Information
AI Technical Summary
Problems solved by technology
Method used
Image
Examples
Embodiment 1
[0037] like figure 1 As shown, the present embodiment discloses a device for measuring Z-axis vibration displacement, which includes an installation base 100, a linear motor 200 and a displacement sensor 300. The stator 210 of the linear motor 200 is arranged on the installation base 100, and the displacement sensor 300 It is used to measure the relative displacement of the mover 220 and the stator 210 of the linear motor 200 .
[0038] In this embodiment, the direction perpendicular to the horizontal ground is the Z axis, such as figure 1 As shown, a linear motor 200 is arranged along the Z-axis, and the mover 220 of the linear motor 200 slides in the Z-axis direction.
[0039] When the linear motor 200 is activated, the magnitude of the magnetic field force on the mover 220 in the Z-axis direction is greater than or equal to the magnitude of the mover 220's own gravity in the Z-axis direction, and the direction is opposite, and the mover 220 maintains a suspension with a su...
Embodiment 2
[0044] like figure 2 , image 3 and Figure 4 As shown, this embodiment discloses a device for measuring Z-axis vibration displacement, which includes a mounting base 100 , a linear motor 200 , a displacement sensor 300 , a limit switch 400 and a mass 500 .
[0045] Specifically, as figure 2 and image 3As shown, the mounting base 100 of this embodiment includes a mounting base 110 and a housing shield 120 , the mounting base 110 is a rectangular flat plate, and the housing shield 120 is a hollow rectangular cover with one end open.
[0046] The stator 210 of the linear motor 200 of the present embodiment is vertically fixed on the installation base 110, and the housing shield 120 is covered on the installation base 110, forming a closed shielding space inside, and the linear motor 200 and the displacement sensor 300 are all located in the housing shield 120 internal.
[0047] Exemplarily, the displacement sensor 300 of this embodiment selects the grating scale, and the...
Embodiment 3
[0058] like Figure 1-8 As shown, this embodiment discloses a method for measuring Z-axis vibration displacement: a linear motor 200 and a displacement sensor 300 are arranged on the surface to be measured, the stator 210 of the linear motor 200 is perpendicular to the surface to be measured, and the linear motor 200 The mover 220 is slidably sleeved on the stator 210 . Start the linear motor 200 and the displacement sensor 300, the mover 220 is suspended on the stator 210 under the action of the magnetic field force and its own gravity to keep the absolute position basically unchanged, and the stator 210 and the mover of the linear motor 200 are monitored by the displacement sensor 300 220 relative displacement data, so as to obtain the vibration displacement data of the surface to be measured.
[0059] Specifically, in this embodiment, the linear motor 200 and the displacement sensor 300 can be pre-assembled on an installation base 100 to form a device for measuring Z-axis ...
PUM
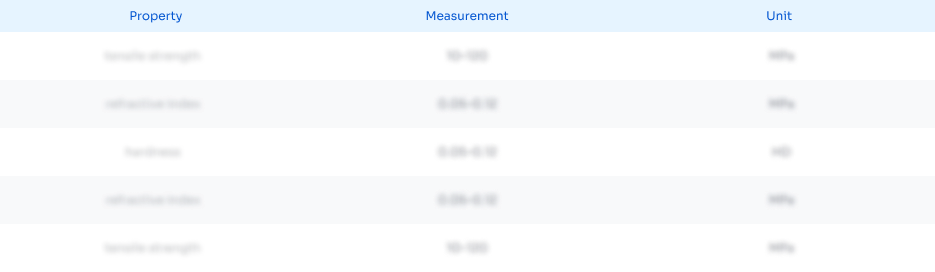
Abstract
Description
Claims
Application Information

- R&D
- Intellectual Property
- Life Sciences
- Materials
- Tech Scout
- Unparalleled Data Quality
- Higher Quality Content
- 60% Fewer Hallucinations
Browse by: Latest US Patents, China's latest patents, Technical Efficacy Thesaurus, Application Domain, Technology Topic, Popular Technical Reports.
© 2025 PatSnap. All rights reserved.Legal|Privacy policy|Modern Slavery Act Transparency Statement|Sitemap|About US| Contact US: help@patsnap.com