Multi-wire array-laser three-dimensional scanning system and multi-wire array-laser three-dimensional scanning method
A laser 3D and scanning system technology, applied in the field of 3D scanning of object surface geometry, can solve the problems of large data noise, reduced accuracy, and difficult to accurately control the working distance, and achieve high reliability.
- Summary
- Abstract
- Description
- Claims
- Application Information
AI Technical Summary
Problems solved by technology
Method used
Image
Examples
Embodiment Construction
[0047] The following will clearly and completely describe the technical solutions in the embodiments of the present invention with reference to the accompanying drawings in the embodiments of the present invention. Obviously, the described embodiments are only some, not all, embodiments of the present invention. Based on the embodiments of the present invention, all other embodiments obtained by persons of ordinary skill in the art without making creative efforts belong to the protection scope of the present invention.
[0048] First, the multi-line array laser three-dimensional scanning system in this application is described as follows: figure 1 As shown, the multi-line array laser three-dimensional scanning system includes a programmable gate array FPGA, at least one stereoscopic image sensor, an inertial sensor, a line laser array, an error feedback controller and a host computer, which can be understood as a control device , for example: upper computer. It has the functi...
PUM
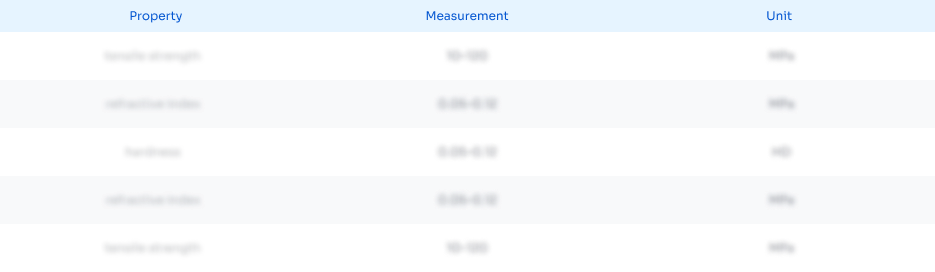
Abstract
Description
Claims
Application Information

- R&D
- Intellectual Property
- Life Sciences
- Materials
- Tech Scout
- Unparalleled Data Quality
- Higher Quality Content
- 60% Fewer Hallucinations
Browse by: Latest US Patents, China's latest patents, Technical Efficacy Thesaurus, Application Domain, Technology Topic, Popular Technical Reports.
© 2025 PatSnap. All rights reserved.Legal|Privacy policy|Modern Slavery Act Transparency Statement|Sitemap|About US| Contact US: help@patsnap.com