Planetary gear transmission mechanism, robot joint reducer and robot
A planetary gear transmission, robot joint technology, applied in the direction of gear transmission, transmission, belt/chain/gear, etc., can solve the problems of high processing precision, high cost, increased cost, etc., and achieves reduced processing difficulty and production. Cost reduction, cost reduction effect
- Summary
- Abstract
- Description
- Claims
- Application Information
AI Technical Summary
Problems solved by technology
Method used
Image
Examples
Embodiment 1
[0034] Such as figure 1 As shown, a planetary gear transmission mechanism includes an input part, a small tooth difference transmission part and an output part, the input part includes a sun gear 1, and 2 to 3 planetary gears 2 driven by the sun gear 1;
[0035]The few-tooth-difference transmission part includes a first ring gear 3, a second ring gear 4, a pair of few-tooth differential wheels 5 meshing with the two ring gears with few teeth differences respectively, and 2 to 3 central axes that are in contact with the two ring gears. The crankshaft 6 arranged parallel to the central axis of the sun gear 1. The teeth of the two internal ring gears and the two few-tooth differential wheels 5 are all inclined-plane involute teeth with variable tooth thickness, that is, the teeth are inclined-plane teeth, which are roughly conical, and the tooth surfaces can also be in the axial direction. Contact, when this kind of gear is mated, a pulling force or pressure is applied on the si...
Embodiment 2
[0046] like figure 2 As shown, a robot joint reducer based on the aforementioned planetary gear transmission mechanism includes a first shell 12, a second shell 13 and a housing 11, and the two shells are respectively rotatably fitted to the said shell through tapered roller bearings 15. On the two sides of the housing 11, the two shells are fixedly connected by pins and bolts. As a whole, the movement and power output after deceleration and torque increase are provided. A lip shape is set between the shell 11 and the two shells. Seal 17 to prevent oil leakage.
[0047] The first ring gear 3 and the second ring gear 4 are both arranged on the inner ring of the housing 11, and a pair of the differential gears with few teeth 5 are arranged between the two shells and respectively connected to the two ring gears. Meshing with few teeth differences forms a mechanism with few teeth differences, which plays a major role in deceleration and torque increase.
[0048] Wherein, the te...
Embodiment 3
[0057] like image 3 As shown, the bearings installed on the two ends of the crankshaft and the two shells can be replaced by rolling elements 21 with retainers. The rolling elements 21 are axially positioned by the circlip 24 installed on the crankshaft. The bearings between the shells become angular contact ball bearings 23, and the two shells simultaneously function as the outer rings of the bearings, simplifying the structure, further reducing the volume, and reducing the cost. In this embodiment, the anti-backlash elastic body 22 floats Installed between two differential wheels with few teeth, it is a ring structure covering the inner side of the entire differential wheel with few teeth.
PUM
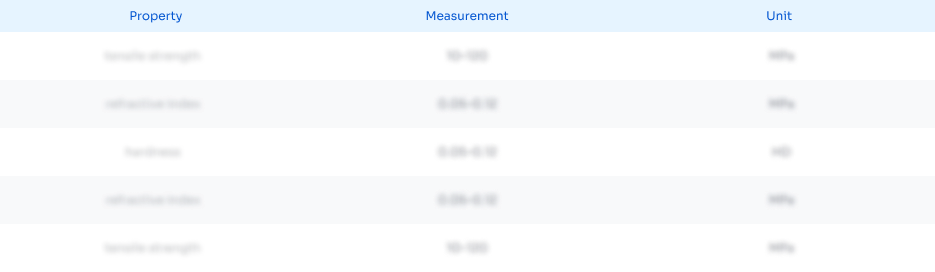
Abstract
Description
Claims
Application Information

- R&D
- Intellectual Property
- Life Sciences
- Materials
- Tech Scout
- Unparalleled Data Quality
- Higher Quality Content
- 60% Fewer Hallucinations
Browse by: Latest US Patents, China's latest patents, Technical Efficacy Thesaurus, Application Domain, Technology Topic, Popular Technical Reports.
© 2025 PatSnap. All rights reserved.Legal|Privacy policy|Modern Slavery Act Transparency Statement|Sitemap|About US| Contact US: help@patsnap.com