High-quality calcium oxide production process and equipment
A production device, calcium oxide technology, applied in lime production, etc., can solve the problems of low quality calcium oxide, calcium oxide is easy to be mixed with ash, easy to occur raw burning and overburning, etc., to achieve high quality, good synchronization, Effect of saving calcination cost
- Summary
- Abstract
- Description
- Claims
- Application Information
AI Technical Summary
Problems solved by technology
Method used
Image
Examples
Embodiment 1
[0026] Embodiment 1: a kind of high-quality calcium oxide production process:
[0027] The first step is to select calcite as raw material, wash and drain;
[0028] In the second step, the calcite is pulverized, and the calcite particles close to the particle size are screened out for subsequent use;
[0029] In the third step, the calcite raw material is sent to a shuttle kiln for calcination, followed by low-temperature calcination at 200-400°C for 4-6 hours, medium-temperature calcination at 400-900°C for 5-7 hours, and high-temperature calcination at 900-1200°C for 4-4 hours. 6 hours, calcination at a constant temperature of 1200°C for 18-25 hours, closed and stored at a constant temperature for 4-6 hours, and cooling for 4-6 hours. About 1 hour, calcination at a high temperature of about 1000°C for about 5 hours, calcination at a constant temperature of 1200°C for about 22 hours, closed storage at a constant temperature for about 5 hours, and cooling for about 5 hours; ...
Embodiment 2
[0035] Embodiment 2: a kind of high-quality calcium oxide production process:
[0036] The first step is to select calcite as raw material, wash and drain;
[0037] In the second step, the calcite is pulverized, and the calcite particles close to the particle size are screened out for subsequent use;
[0038] In the third step, the calcite raw material is sent to a shuttle kiln for calcination, followed by low-temperature calcination at 200-400°C for 4-6 hours, medium-temperature calcination at 400-900°C for 5-7 hours, and high-temperature calcination at 900-1200°C for 4-4 hours. 6 hours, calcination at a constant temperature of 1200°C for 18-25 hours, closed and stored at a constant temperature for 4-6 hours, and cooling for 4-6 hours. About 1 hour, calcination at a high temperature of about 1000°C for about 5 hours, calcination at a constant temperature of 1200°C for about 22 hours, closed storage at a constant temperature for about 5 hours, and cooling for about 5 hours; ...
PUM
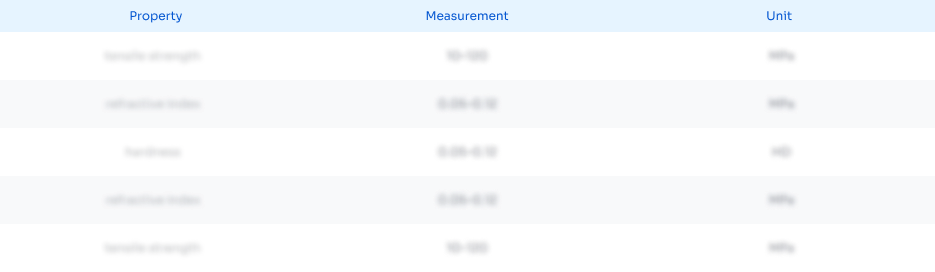
Abstract
Description
Claims
Application Information

- Generate Ideas
- Intellectual Property
- Life Sciences
- Materials
- Tech Scout
- Unparalleled Data Quality
- Higher Quality Content
- 60% Fewer Hallucinations
Browse by: Latest US Patents, China's latest patents, Technical Efficacy Thesaurus, Application Domain, Technology Topic, Popular Technical Reports.
© 2025 PatSnap. All rights reserved.Legal|Privacy policy|Modern Slavery Act Transparency Statement|Sitemap|About US| Contact US: help@patsnap.com