Programming method for airplane thin-wall curved surface skin automatic drilling and riveting
A technology of automatic drilling and riveting and programming method, applied in the direction of instruments, simulators, control/adjustment systems, etc., can solve problems such as poor assembly effect, difficulty in meeting requirements, geometric deformation, etc.
- Summary
- Abstract
- Description
- Claims
- Application Information
AI Technical Summary
Problems solved by technology
Method used
Image
Examples
Embodiment Construction
[0024] see Figure 1-Figure 6 , online teaching: figure 2 For the geometric model diagram of the automatic drilling and riveting machine, the skin is clamped and fixed on the bracket of the drilling and riveting machine, and the laser displacement, vision, and normal sensors installed on the drilling and riveting head are used to measure the skin feature points. The position of each axis completes the normal posture adjustment and position alignment of the drill riveting head to the skin feature point, and then the numerical control system reads out the axis data X, Y, Z1, Z2, A corresponding to the feature point.
[0025] Such as figure 2 As shown, the drilling and riveting machine consists of five machine axes X, Y, Z1, Z2, and A, which are not standard geometric axes X, Y, Z, A, and B. Because when Z1 and Z2 move synchronously, a translation axis Z is formed. When Z1 and Z2 move asynchronously, not only the translation axis Z is synthesized but also the rotation axis B ...
PUM
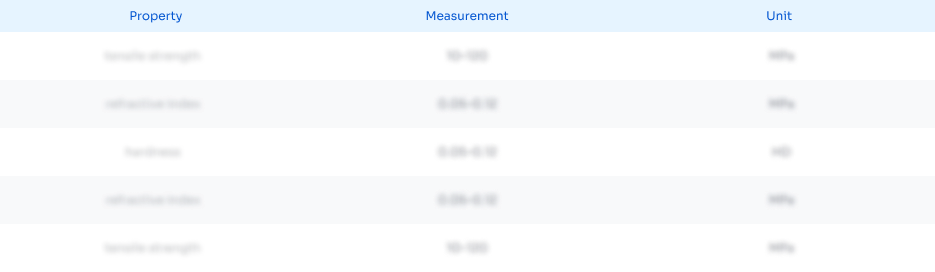
Abstract
Description
Claims
Application Information

- Generate Ideas
- Intellectual Property
- Life Sciences
- Materials
- Tech Scout
- Unparalleled Data Quality
- Higher Quality Content
- 60% Fewer Hallucinations
Browse by: Latest US Patents, China's latest patents, Technical Efficacy Thesaurus, Application Domain, Technology Topic, Popular Technical Reports.
© 2025 PatSnap. All rights reserved.Legal|Privacy policy|Modern Slavery Act Transparency Statement|Sitemap|About US| Contact US: help@patsnap.com