Spatial two-point calibration projection based base coordinate system calibration method of coordinated robot
A technology of base frame and calibration method, which is applied in the field of collaborative robot base frame calibration based on spatial two-point projection
- Summary
- Abstract
- Description
- Claims
- Application Information
AI Technical Summary
Problems solved by technology
Method used
Image
Examples
Embodiment Construction
[0065] The present invention will be described in further detail below in conjunction with the accompanying drawings and specific embodiments.
[0066] The basic principle of the present invention mainly lies in: arbitrarily determine two non-repetitive calibration points on different sides of the line connecting the origins of the base coordinates of the two cooperative robots and in the overlapping public work space, and by constructing the action of shaking hands of the robots, the two The end point of the collaborative robot arrives at the calibration point at the same time in any spatial position, and the collaborative robot system and the determined calibration point are projected on the X-Y, Y-Z plane, and the projected geometric constraint relationship diagram of the plane is established, so as to obtain the base of the collaborative robot The rotation and translation offsets of the relative poses of the coordinate system, and finally obtain the pose transformation matr...
PUM
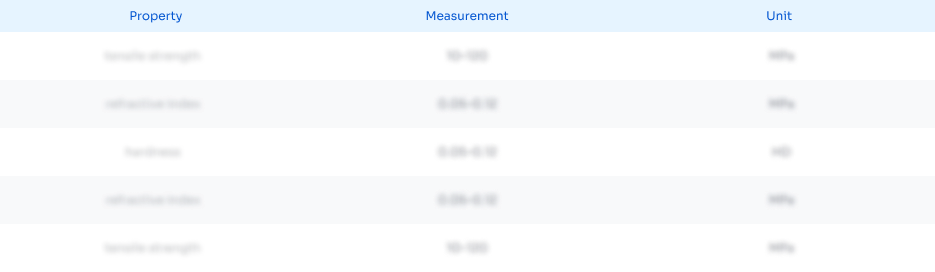
Abstract
Description
Claims
Application Information

- R&D
- Intellectual Property
- Life Sciences
- Materials
- Tech Scout
- Unparalleled Data Quality
- Higher Quality Content
- 60% Fewer Hallucinations
Browse by: Latest US Patents, China's latest patents, Technical Efficacy Thesaurus, Application Domain, Technology Topic, Popular Technical Reports.
© 2025 PatSnap. All rights reserved.Legal|Privacy policy|Modern Slavery Act Transparency Statement|Sitemap|About US| Contact US: help@patsnap.com