Hydraulic braking system
A braking system, braking device technology, applied in elevators, transportation and packaging, etc., can solve the problems of high energy demand, high energy consumption, expensive use of accumulators and regulating valves, etc.
- Summary
- Abstract
- Description
- Claims
- Application Information
AI Technical Summary
Problems solved by technology
Method used
Image
Examples
Embodiment Construction
[0033] figure 1 A people transport system 1 is shown with a brake system 2 , which is designed as an elevator (lift system) 1 . In a correspondingly modified embodiment, the people transport device 1 can also be designed as an escalator or a moving walkway.
[0034] The people conveyor 1 has an elevator car 33 . The elevator car 33 is suitable for accommodating people or goods. The elevator car 33 is connected in the example to a counterweight 35 by means of a carrier mechanism 36 via a drive 37 . The elevator car 33 is guided on the guide rail 3 by means of guide shoes 34 . The guide rail 3 comprises a rail seat and a guiding and braking web 4 . The rail mounts of the guide rails 3 can be connected, for example, in the elevator shaft of the elevator 1 to a wall of the elevator shaft or to a suitable support structure. In this case, the braking system 2 corresponds to the braking web 4 of the guide rail 3 . In general, a pair of guide rails 3 is used in such a people con...
PUM
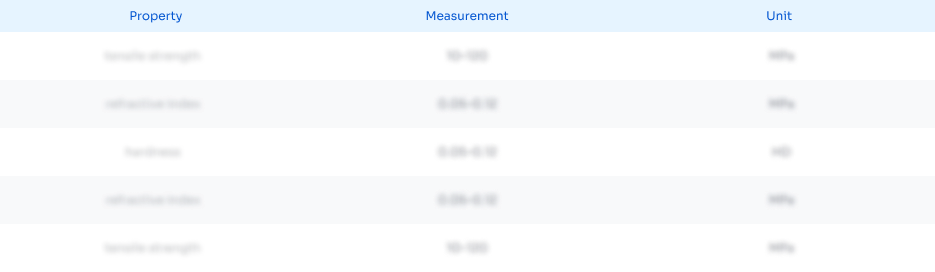
Abstract
Description
Claims
Application Information

- R&D
- Intellectual Property
- Life Sciences
- Materials
- Tech Scout
- Unparalleled Data Quality
- Higher Quality Content
- 60% Fewer Hallucinations
Browse by: Latest US Patents, China's latest patents, Technical Efficacy Thesaurus, Application Domain, Technology Topic, Popular Technical Reports.
© 2025 PatSnap. All rights reserved.Legal|Privacy policy|Modern Slavery Act Transparency Statement|Sitemap|About US| Contact US: help@patsnap.com