Soft robotic bionic fingers
A robot and finger technology, applied in the field of flexible robot bionic fingers, can solve the problems of complex mechanical structure, high cost, easy damage, etc., and achieve the effect of low control difficulty, simple structure, and not easy to deform.
- Summary
- Abstract
- Description
- Claims
- Application Information
AI Technical Summary
Problems solved by technology
Method used
Image
Examples
Embodiment Construction
[0025] Such as figure 1 As shown, the flexible robotic bionic finger of the present invention includes a shell 1 and an airbag 2, and the airbag 2 is elastic.
[0026] Such as figure 2 As shown, the flexible robot bionic finger shell 1 of the present invention comprises a fingertip shell 11, an elastic knuckle cover 12, an intermediate connecting shell 13, and a root shell 14; the fingertip shell 11 is connected to the intermediate connecting shell 13 through the elastic knuckle cover 12, and the intermediate connecting shell 13 is connected to the root shell 14 through the elastic joint sleeve 12 to form an integrated chamber. Compatible with the shape of the joint.
[0027] Such as image 3 As shown, one end of the fingertip shell 11 can be closed as the top of the shell, and the other end can be used as the bottom of the fingertip shell 11. The bottom of the fingertip shell 11 can be cross-cut or beveled to form two sides with different axial lengths. Either side is us...
PUM
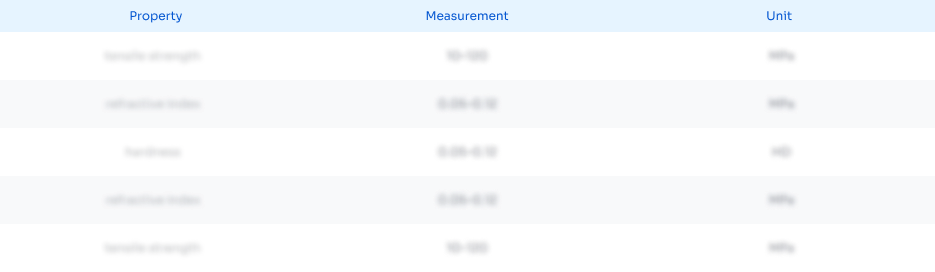
Abstract
Description
Claims
Application Information

- R&D Engineer
- R&D Manager
- IP Professional
- Industry Leading Data Capabilities
- Powerful AI technology
- Patent DNA Extraction
Browse by: Latest US Patents, China's latest patents, Technical Efficacy Thesaurus, Application Domain, Technology Topic, Popular Technical Reports.
© 2024 PatSnap. All rights reserved.Legal|Privacy policy|Modern Slavery Act Transparency Statement|Sitemap|About US| Contact US: help@patsnap.com