Extrinsic fiber Fabry-Perot acceleration sensor based on 45-degree fiber and processing method thereof
A technology of acceleration sensor and processing method, which is applied in the direction of using inertial force for acceleration measurement, etc., can solve the problems of poor stability of coaxial extrinsic fiber optic Fibonacci cavity acceleration sensor, etc., and achieves a reduction in size and cavity length. Effect
- Summary
- Abstract
- Description
- Claims
- Application Information
AI Technical Summary
Problems solved by technology
Method used
Image
Examples
specific Embodiment 1
[0036] This embodiment is a device embodiment of an extrinsic fiber-optic FAP acceleration sensor based on a 45° optical fiber.
[0037] The extrinsic fiber-optic FAPP acceleration sensor based on the 45° optical fiber of the present embodiment has a structural schematic diagram as figure 1 shown. The sensor includes a silicon support structure 1, an optical fiber 2 with a polished end face of 45° inserted from the side of the silicon support structure 1 against the bottom, a quality block 3 arranged on the top of the silicon support structure 1, the silicon support structure 1 and the mass The block 3 constitutes a enamel cavity; the mass block 3 is thick in the middle and thin around, and the lower surface of the mass block 3 is coated with a reflective film.
specific Embodiment 2
[0038] This embodiment is a device embodiment of an extrinsic fiber-optic FAP acceleration sensor based on a 45° optical fiber.
[0039] The extrinsic fiber-optic FAP acceleration sensor based on 45° optical fiber in this embodiment, on the basis of the specific embodiment 1, further defines that a circular protrusion is arranged in the middle of the proof mass 3 . It is set as a circular protrusion, so that its vibration has isotropic characteristics, which is beneficial to improve the repeatability of measurement results.
specific Embodiment 3
[0040] This embodiment is an embodiment of the processing method of the extrinsic optical fiber FPP acceleration sensor based on the 45° optical fiber.
[0041] The processing method of the extrinsic fiber optic FAPP acceleration sensor based on the 45° optical fiber, the process flow chart is as follows figure 2 shown. The method includes the following steps:
[0042] Step a, processing the silicon support structure 1 provided with the optical fiber socket;
[0043] Step b, processing the quality block 3 coated with a reflective film on the lower surface;
[0044] The steps a and b are carried out synchronously or in any order;
[0045] Step c, bonding the top of the silicon support structure 1 to the surface of the mass block 3 coated with a reflective film;
[0046] Step d, insert the optical fiber 2 from the optical fiber socket, and adjust the polished end surface of the optical fiber 2 to form an angle of 45° with the bottom surface of the silicon support structure ...
PUM
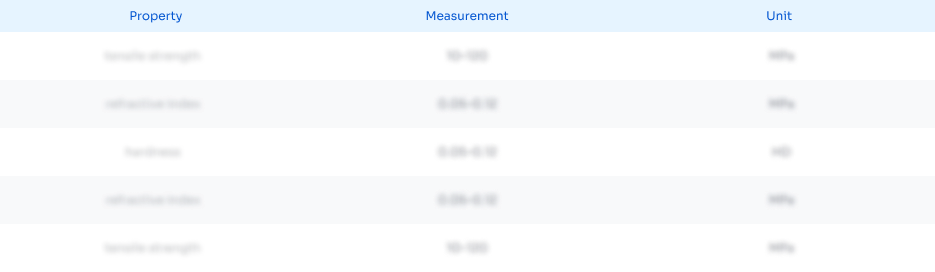
Abstract
Description
Claims
Application Information

- R&D
- Intellectual Property
- Life Sciences
- Materials
- Tech Scout
- Unparalleled Data Quality
- Higher Quality Content
- 60% Fewer Hallucinations
Browse by: Latest US Patents, China's latest patents, Technical Efficacy Thesaurus, Application Domain, Technology Topic, Popular Technical Reports.
© 2025 PatSnap. All rights reserved.Legal|Privacy policy|Modern Slavery Act Transparency Statement|Sitemap|About US| Contact US: help@patsnap.com