Method for measuring aluminum alloy continuous cooling transformation curve
An aluminum alloy and curve technology, which is applied in the field of non-ferrous metal material preparation, can solve the problems of inability to distinguish cooling-induced phase differences, rapid continuous transformation of aluminum alloys, and lack of effective controllable quenching methods and equipment for quenching research.
- Summary
- Abstract
- Description
- Claims
- Application Information
AI Technical Summary
Problems solved by technology
Method used
Image
Examples
Embodiment
[0118] The implementation of the present invention is illustrated with the measurement process of the continuous cooling transition curve of aluminum alloy AA7150 as an example:
[0119] Table 1 shows the models of No. 1 differential scanning calorimeter, No. 2 differential scanning calorimeter, No. 3 differential scanning calorimeter and thermal dilatometer used in the examples and the corresponding sample sizes.
[0120] Table 1. Detailed dimensions and corresponding masses of different samples
[0121] DSC instrument Sample size (mm) Reference sample mass (mg) Perkin Elmer Pyris C Ф6.4X1 83.5 Mettler 823 Ф5.4X1.4 82.4 Seteram 121 Ф6.1(5.7)X22 1742 Dilatometer Ф6.4X1 83.5
[0122]In Table 1, the thermal dilatometer is a quenching thermal dilatometer whose model is DIL805A / D
[0123] Table 2. Chemical composition of AA7150 aluminum alloy
[0124] Fe Si Zn Mg Cu Cr mn Zr Al 0.05 0.02 6.33 2.15 2...
PUM
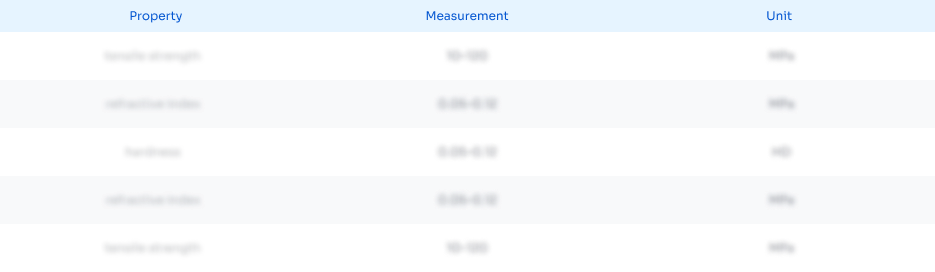
Abstract
Description
Claims
Application Information

- R&D Engineer
- R&D Manager
- IP Professional
- Industry Leading Data Capabilities
- Powerful AI technology
- Patent DNA Extraction
Browse by: Latest US Patents, China's latest patents, Technical Efficacy Thesaurus, Application Domain, Technology Topic, Popular Technical Reports.
© 2024 PatSnap. All rights reserved.Legal|Privacy policy|Modern Slavery Act Transparency Statement|Sitemap|About US| Contact US: help@patsnap.com