Boiler tail exhaust gas heat utilization system
A flue gas and boiler technology, which is applied in the field of the heat utilization system of the flue gas at the tail of the boiler, can solve the problems of limited working capacity, little effect of boiler efficiency, and inability to reduce the exhaust gas temperature and boiler efficiency, etc., so as to improve stable ignition and flexible layout. and convenience, the effect of guaranteed performance
- Summary
- Abstract
- Description
- Claims
- Application Information
AI Technical Summary
Problems solved by technology
Method used
Image
Examples
Embodiment 1
[0033] When arranging the preheater and economizer according to the first arrangement above, take a 1000MW ultra-supercritical coal-fired boiler as an example to illustrate the load as the rated load, as follows figure 1As shown, the 490°C high-temperature flue gas discharged from the tail flue of the boiler first flows through the high-temperature economizer 4, exchanges heat with the boiler feed water flowing through it, and leaves after the temperature drops to 426°C. Then it enters the high-temperature preheater 1, where it heats the secondary air. After the temperature drops to 395°C, it leaves and flows through the catalyst 6. The catalyst is a denitration catalyst that reduces most of the nitric oxide in the flue gas to nitrogen. Subsequently, the flue gas enters the medium-temperature economizer 5, where the boiler feed water is heated, and the temperature drops to 347°C before leaving. Then, the flue gas enters the medium temperature preheater 2. The medium temperatu...
PUM
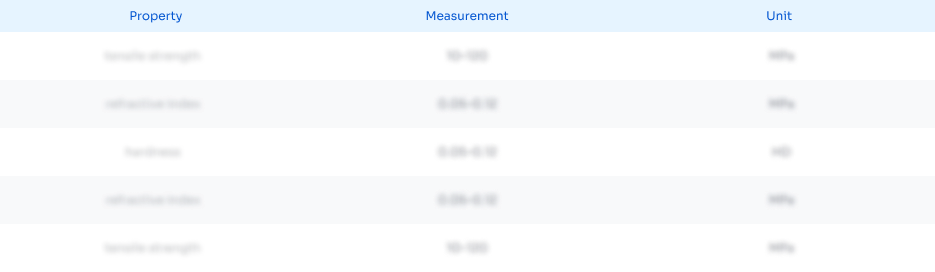
Abstract
Description
Claims
Application Information

- Generate Ideas
- Intellectual Property
- Life Sciences
- Materials
- Tech Scout
- Unparalleled Data Quality
- Higher Quality Content
- 60% Fewer Hallucinations
Browse by: Latest US Patents, China's latest patents, Technical Efficacy Thesaurus, Application Domain, Technology Topic, Popular Technical Reports.
© 2025 PatSnap. All rights reserved.Legal|Privacy policy|Modern Slavery Act Transparency Statement|Sitemap|About US| Contact US: help@patsnap.com