Manufacturing method and tool for silicon rubber mold of landscape material
A technology for manufacturing tooling and manufacturing method, applied in the field of mold processing and forming, can solve the problems of short service life, inconvenient demoulding, rigid texture, etc., and achieve the effect of long service life, convenient demoulding, and natural mold surface texture
- Summary
- Abstract
- Description
- Claims
- Application Information
AI Technical Summary
Problems solved by technology
Method used
Image
Examples
Embodiment 1
[0018] A method for manufacturing a silicone mold for landscape materials. The manufacturing method includes the following steps:
[0019] a. Fix the original wooden parts that have been carbonized for 30-40 minutes on the bottom plate;
[0020] b. Apply the release agent evenly on the surface of the bottom plate, the original part and the mold frame. After the painting is completed, buckle the mold frame above the original part and fix it;
[0021] c. Mix the silica gel material liquid and the curing agent in a ratio of 1:0.8, and stir for 2 minutes to fully mix;
[0022] d. Pour the mixed silica gel liquid and curing agent into the mold frame. In order to avoid the deterioration of fluidity and affect the infusion effect, the infusion process is controlled within 5 minutes;
[0023] e. Let the poured silica gel and curing agent stand for 24 hours to fully cure;
[0024] f. Demould, take the cured silicone mold out of the mold frame.
Embodiment 2
[0026] A method for manufacturing a silicone mold for landscape materials. The manufacturing method includes the following steps:
[0027] a. Fix the original wooden parts that have been carbonized for 30-40 minutes on the bottom plate;
[0028] b. Apply the release agent evenly on the surface of the bottom plate, the original part and the mold frame. After the painting is completed, buckle the mold frame above the original part and fix it;
[0029] c. Mix the silica gel material liquid and the curing agent at a ratio of 1:1, and stir for 2 minutes to fully mix;
[0030] d. Pour the mixed silica gel liquid and curing agent into the mold frame. In order to avoid the deterioration of fluidity and affect the infusion effect, the infusion process is controlled within 5 minutes;
[0031] e. Let the poured silica gel and curing agent stand for 18 hours to fully cure;
[0032] f. Demould, take the cured silicone mold out of the mold frame.
PUM
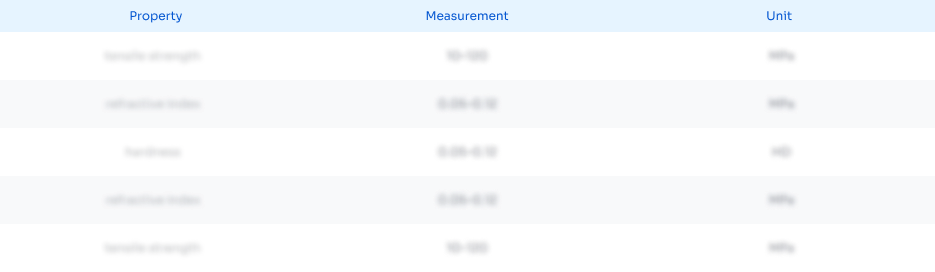
Abstract
Description
Claims
Application Information

- R&D
- Intellectual Property
- Life Sciences
- Materials
- Tech Scout
- Unparalleled Data Quality
- Higher Quality Content
- 60% Fewer Hallucinations
Browse by: Latest US Patents, China's latest patents, Technical Efficacy Thesaurus, Application Domain, Technology Topic, Popular Technical Reports.
© 2025 PatSnap. All rights reserved.Legal|Privacy policy|Modern Slavery Act Transparency Statement|Sitemap|About US| Contact US: help@patsnap.com