a mill
A pulverizer and mill technology, which is applied in grain processing and other directions, can solve the problems of difficult cooling, large amount of returned material, affecting output, etc., and achieve the effect of extending the life of the connection, reducing the transmission of vibration, and saving production costs.
- Summary
- Abstract
- Description
- Claims
- Application Information
AI Technical Summary
Problems solved by technology
Method used
Image
Examples
Embodiment 1
[0030] Embodiment 1, a kind of pulverizer, with reference to figure 1 , figure 2 , image 3, is that the automatic feeding machine 2, particle barrel 3, and vibrating feeder 4 connected in sequence are fixed on the frame 1, and the vibrating feeder 4 is connected to the mill 6 fixed on the frame 1 through the feeding pipe 5 The feeding port 611 of the mill 6 is connected with a suction pipe 7, and the suction pipe 7 is connected with the combined shut-off fan 8 through the cyclone separator 9, and the fan 10 fixed on the frame 1 passes through the suction pipe 11 Connect with the cyclone separator 9, the rotating frame 12 is fixed on the fixed plate on the frame 1, the main and auxiliary shafts of the rotating frame 12 are provided with a counterweight 13, the separating screen 14 is installed in the rotating frame 12, and the separating screen 14 The feed port is connected with the lower port of the combined shut-off fan 8 through a soft interface, the discharge port of th...
Embodiment 2
[0031] Embodiment 2, a kind of pulverizer, with reference to Figure 1 to Figure 6 , on the basis of Embodiment 1, the upper air channel 612 for cooling the outer side of the upper cutter head is provided with a fixed seat annular notch 615 on the fixed seat 65, and the fixed seat annular notch 615 makes the upper air channel air inlet 616 It communicates with the gap between the fixed seat 65 and the upper cutter head 64, and the gap between the fixed seat 65 and the upper cutter head 64 communicates with the upper air duct air outlet 618. The upper air duct air inlet 616 is arranged on the upper cover 66, and the fixed seat is annular. The notch 615 is arranged on the fixed seat 65 close to the main shaft 61, and the upper air channel air outlet 618 is arranged on the outer circumference of the fixed seat 65, and the middle air channel 613 used for cooling the upper cutter head and the lower cutter head is based on The feed port 611 is used as the air inlet of the middle air...
Embodiment 3
[0032] Embodiment 3, a kind of pulverizer, with reference to Figure 1 to Figure 7 , on the basis of Embodiment 2, the upper end of the suspension rod 74 is fixed on the fixed plate 71 through the joint bearing 72, and the lower end of the suspension rod 74 is fixed on the support welding plate 710 through the joint bearing 72, and the support welding plate 710 is connected with the rotating frame 12 are welded as a whole, the motor 713 is fixed on the rotating frame 12, the main shaft 76 and the auxiliary shaft 77 installed on different sides of the rotating frame 12 are installed on the rotating frame 12 through the bearing seat, and the counterweight iron 13 is installed on the main shaft 76 and the auxiliary shaft 77 , the motor 713 drives the main shaft 76 to rotate, and the main shaft 76 is connected to drive the auxiliary shaft 77 to rotate synchronously through the synchronous belt 75, and the others are exactly the same as in the second embodiment.
PUM
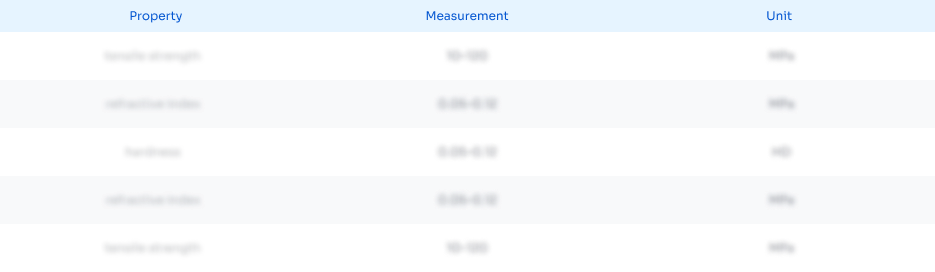
Abstract
Description
Claims
Application Information

- R&D
- Intellectual Property
- Life Sciences
- Materials
- Tech Scout
- Unparalleled Data Quality
- Higher Quality Content
- 60% Fewer Hallucinations
Browse by: Latest US Patents, China's latest patents, Technical Efficacy Thesaurus, Application Domain, Technology Topic, Popular Technical Reports.
© 2025 PatSnap. All rights reserved.Legal|Privacy policy|Modern Slavery Act Transparency Statement|Sitemap|About US| Contact US: help@patsnap.com